Crowning System
High Precision & Motorized Crowning System
CAMT®️Mechanical Compensation in Press Brakes: Precision, Efficiency, and Cost-Effectiveness
CAMT® Automatic Defelection Compensation:
Mechanical compensation in press brakes effectively mitigates equipment deformation through physical adjustments, ensuring precision and consistency in bending operations. Its advantages include high accuracy, cost-effectiveness, ease of use, and broad applicability, making it ideal for efficient and stable production environments. Compared to alternatives like hydraulic compensation, mechanical compensation offers advantages in maintenance and cost, though it may require integration with CNC systems for optimal performance in highly precise or complex scenarios.
Advantage:
- Ensures consistent bending angles by counteracting ram and worktable deformation, ideal for long workpieces and high-accuracy tasks.
- Simpler design with lower maintenance costs compared to hydraulic or CNC compensation, suitable for budget-conscious operations.
- Compatible with various materials and thicknesses, offering broad applicability.
- Automated compensation minimizes setup time, boosting production efficiency.
- Automatic systems integrated with CNC reduce operator skill requirements.
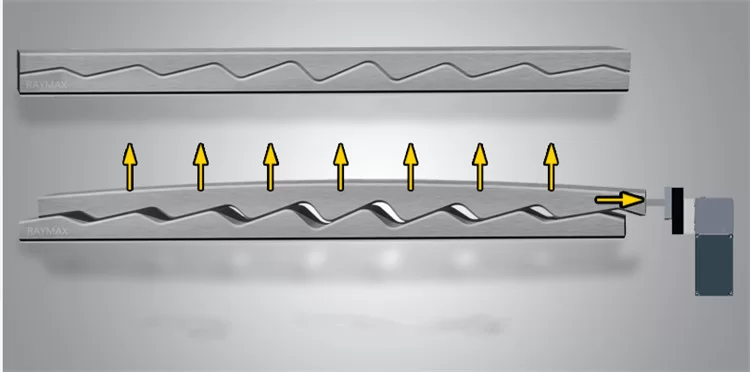
Mechanic Compensation
Benefits of Mechanical Compensation with Precise Effectiveness and Multi-Point Crowning
- Reduces Deformation: Counteracts worktable and slider distortion from applied forces, ensuring consistent bending angles and enhanced machining accuracy, especially for long and varied workpieces.
- Improves Precision: Multi-point mechanical crowning allows independent adjustments across the worktable’s length, precisely managing deformation in each section for superior straightness and uniformity in extended workpieces.
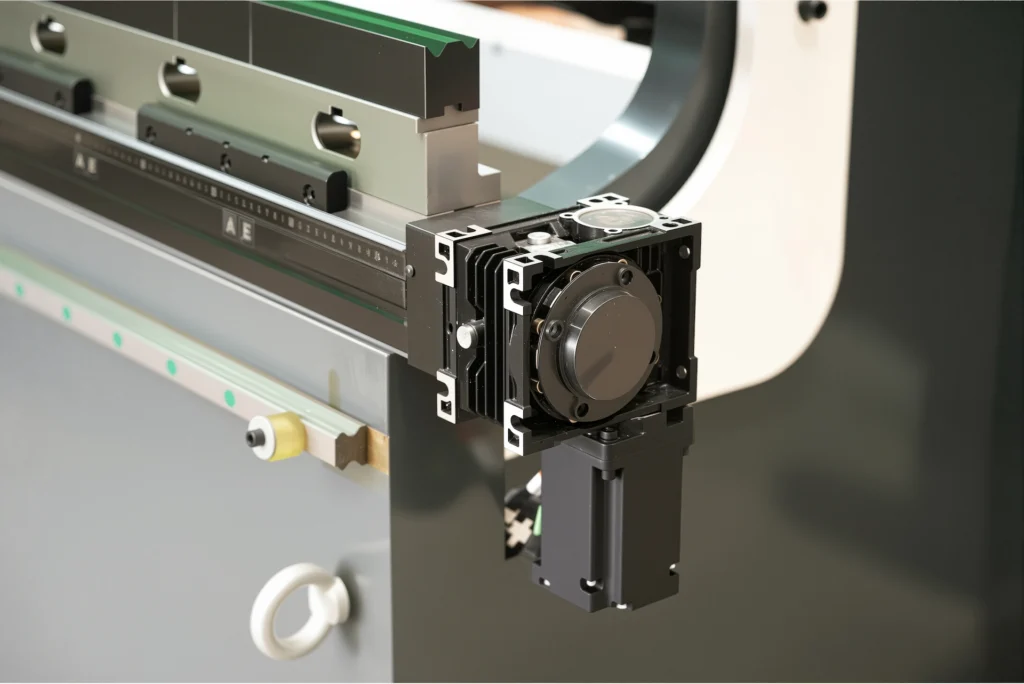
Benefits of Electric Motorized Crowning
- Addresses bending or sagging in the worktable and slider caused by applied forces, particularly at the center, ensuring consistent results.
- Utilizes a system of movable wedges or supports to pre-adjust or dynamically alter the worktable’s shape for optimal performance.
- Automatically or manually adjusts based on material thickness, length, and bending force to maintain precision.
- Maintains a consistent gap between upper and lower dies, delivering even bending angles across the entire workpiece.
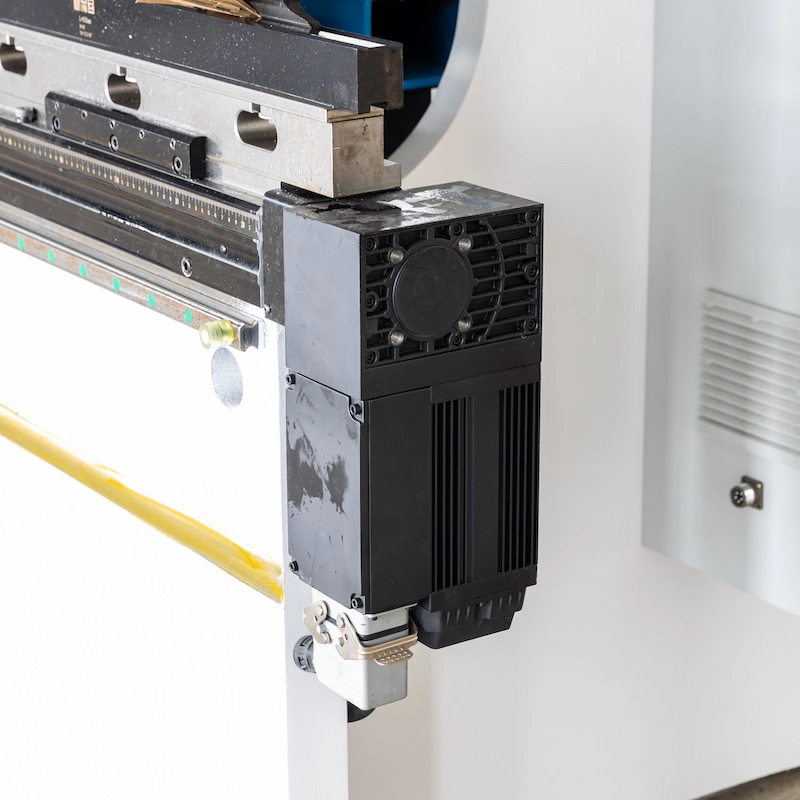