How to Choose the Right Sheet Metal Press Brake
Selecting the right sheet metal press brake is critical for achieving precision, efficiency, and quality in manufacturing projects, whether for automotive parts, electrical enclosures, or structural components. With options like hydraulic and servo press brakes, understanding their differences and aligning them with your needs is key. This comprehensive guide compares hydraulic and servo press brakes, covers worktable and mold selection, precision, operation, maintenance, and manufacturer support, and includes real-world insights to help you make an informed decision.
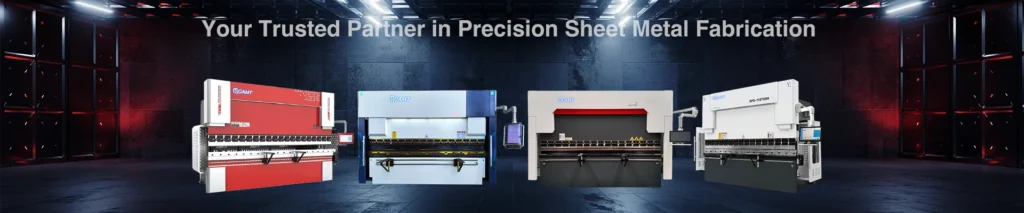
Hydraulic vs. Servo Press Brakes: A Detailed Comparisons.
Hydraulic Press Brake
Hydraulic press brakes use hydraulic cylinders to deliver powerful bending force, making them a staple in sheet metal fabrication for their versatility and robustness.
Key Features
Hydraulic System: Generates high force via hydraulic fluid, ideal for thick sheets (e.g., 5–20 mm steel).
Adjustable Tooling: Supports diverse upper and lower dies for various sheet thicknesses and bend shapes.
Consistent Pressure: Ensures stable, uniform bending for consistent results.
Advantages
Heavy-Duty Capability: Excels at bending thick or high-strength materials like stainless steel.
Versatility: Handles materials such as mild steel, aluminum, and copper for applications in automotive, construction, and appliances.
CNC Automation: Modern models with CNC systems offer programmable precision and efficiency.
Cost-Effective: Lower initial cost (e.g., $5,000-$100,000) compared to servo models, per industry data from Thomasnet.
Working Principle
Hydraulic Drive: Cylinders powered by hydraulic oil move the ram to press the sheet into the lower die.
Mold System: Upper and lower dies form V-shapes or custom profiles for bending.
Pressure Control: Adjustable hydraulic pressure ensures precise force for different materials, adhering to ASME B5.52 standards.
Applications
Manufacturing automotive panels, HVAC ducts, and structural frames.
Producing custom metal parts like brackets, casings, and enclosures.
Supporting high-volume production with diverse bending needs.
Maintenance and Care
Regular Checks: Monitor hydraulic oil levels and pressure weekly to prevent leaks or performance issues.
Cleaning: Remove metal shavings from dies and worktables to maintain accuracy.
Oil Replacement: Change hydraulic fluid every 6–12 months, depending on usage, to ensure system reliability.
Pros and Cons
Pros: Handles thick sheets, supports complex bends, cost-effective for small to large shops.
Cons: Higher maintenance (e.g., $1,000-$5,000 annually, per The Fabricator), less energy-efficient, slightly lower precision (±0.1 mm) than servo models.
Choosing a Hydraulic Press Brake
Select based on bending capacity (e.g., 50–500 tons), worktable length (e.g., 2–6 meters), and maximum sheet thickness (e.g., up to 20 mm). CNC models are ideal for high precision. Choose V-dies or custom molds based on bend requirements.
Servo Press Brake
Servo press brakes leverage electric servo motors for precise, energy-efficient bending, making them ideal for modern, high-precision manufacturing.
Key Features
Servo Motor Drive: Electric motors ensure accurate ram positioning with rapid response.
High Precision: Achieves tolerances as tight as ±0.01 mm, per Bystronic specifications.
Energy Efficiency: Consumes power only during operation, reducing energy costs by up to 50%.
Advantages
Superior Accuracy: Perfect for aerospace, electronics, or medical device components requiring exact bends.
Energy Savings: Lower running costs, with energy consumption 30–50% less than hydraulic models (Amada data).
Advanced Automation: CNC systems with IoT integration enable smart manufacturing and data tracking.
Low Maintenance: No hydraulic fluid, reducing upkeep costs to $500-$2,000 annually.
Working Principle
Servo Control: Motors drive the ram with precision, controlled by CNC software.
Mold System: Uses upper and lower dies to shape sheet metal, similar to hydraulic brakes.
Programmable Precision: CNC systems allow complex bend sequences and real-time adjustments.
Applications
Precision parts for aerospace (e.g., fuselage panels) and electronics (e.g., enclosures).
High-volume production of intricate sheet metal components.
Small-batch, custom fabrication with frequent setup changes.
Maintenance and Care
Lubrication: Lubricate mechanical components quarterly to ensure smooth operation.
Software Updates: Update CNC firmware regularly for optimal performance.
Cleaning: Keep molds and worktables free of debris to maintain accuracy.
Pros and Cons
Pros: High precision, energy-efficient, low maintenance, supports Industry 4.0 features.
Cons: Higher initial cost ($50,000-$500,000), less suited for very thick sheets (>15 mm).
Choosing a Servo Press Brake
Evaluate bending capacity (e.g., 40–200 tons), worktable size (e.g., 1–4 meters), and precision needs. CNC models with smart features are ideal for complex, high-volume tasks. Select molds compatible with your sheet metal and bend types.
Comparison Table: Hydraulic vs. Servo Press Brakes
Feature | Hydraulic Press Brake | Servo Press Brake |
---|---|---|
Bending Capacity | 50–500 tons, ideal for thick sheets | 40–200 tons, best for thin to medium sheets |
Precision | ±0.1 mm | ±0.01 mm |
Energy Efficiency | Moderate (higher consumption) | High (30–50% less energy) |
Initial Cost | $5,000-$100,000 | $50,000-$500,000 |
Maintenance Cost | $1,000-$5,000/year | $500-$2,000/year |
Applications | Heavy-duty, versatile bending | High-precision, complex parts |
Automation | CNC optional, less advanced | Advanced CNC with IoT integration |
Selecting Worktables and Molds
Hydraulic Press Brake
The mold system determines bend quality and operational efficiency.
Key Considerations:
Compatibility: Ensure molds suit sheet thickness (e.g., 0.5–10 mm) and bend types (e.g., V-dies for 90-degree bends).
Ease of Adjustment: Quick-change molds reduce setup time, boosting productivity.
Durability: High-quality steel molds (e.g., 42CrMo) ensure longevity, per ISO 9001 standards.
Tip: Use standard mold systems (e.g., Amada, Wila) for cost-effective replacements and versatility.
Worktable Dimensions
The worktable must support your sheet metal sizes and production demands.
Key Considerations:
Length: Match worktable length (e.g., 2–6 meters) to your largest sheets.
Load Capacity: Ensure support for heavy sheets (e.g., 500–2,000 kg) without deformation.
Back Gauges: Adjustable back gauges improve positioning accuracy for complex bends.
Tip: Choose a worktable slightly larger than current needs for future scalability.
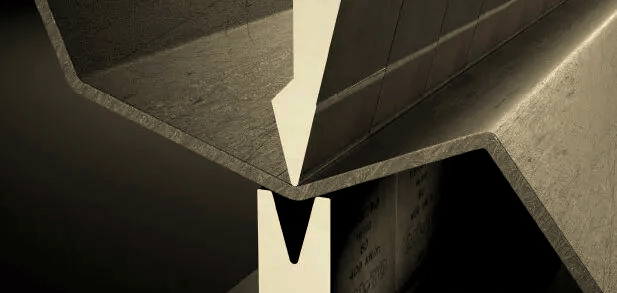
Prioritizing Precision and Repeatability
Positioning Accuracy
High accuracy ensures consistent, high-quality bends.
Key Considerations:
Servo Precision: Achieves ±0.01 mm, ideal for critical applications like aerospace.
Hydraulic Precision: ±0.1 mm, sufficient for general manufacturing.
Repeatability: CNC systems ensure identical bends across batches.
Tip: Request a demo to verify accuracy with your specific materials.
Control System
Advanced controls enhance precision and automation.
Key Considerations:
CNC Systems: Enable programmable bend angles, sequences, and real-time monitoring.
Smart Features: Look for IoT-enabled systems for data analytics and predictive maintenance (e.g., Trumpf’s TruBend systems).
User Interface: Intuitive touch-screen interfaces reduce operator errors.
Tip: Opt for offline programming to streamline setup and reduce downtime.
Operation and Maintenance
Operation Intuitiveness
User-friendly press brakes improve efficiency and reduce training time.
Key Considerations:
Interface: Touch-screen CNC systems with 3D visualization simplify programming.
Training: Ensure manufacturers offer operator training or tutorials.
Tip: Test the interface during a demo to confirm ease of use.
Maintenance Requirements
Low maintenance minimizes downtime and costs.
Key Considerations:
Hydraulic Models: Require regular oil checks, filter replacements, and leak inspections.
Servo Models: Need minimal maintenance, focusing on lubrication and software updates.
Spare Parts: Confirm availability of molds and components for quick repairs.
Tip: Schedule preventive maintenance (e.g., quarterly checks) to extend machine life.
Evaluating Manufacturers and After-Sales Service
Brand Reputation
Choose trusted manufacturers for quality and reliability.
Key Considerations:
Top Brands: Amada (precision), Trumpf (automation), Bystronic (efficiency), Accurpress (affordability).
Industry Feedback: Check reviews on platforms like Thomasnet for user experiences.
Tip: Attend trade shows (e.g., FABTECH) to see machines in action.
Add Your Heading Text Here
After-Sales Support
Robust support ensures long-term performance.
Key Considerations:
Service Network: Local technicians reduce repair downtime.
Warranty: Look for 1–3-year warranties on critical components like rams and motors.
Parts Supply: Ensure fast access to molds and spares via distributors.
Tip: Request detailed service contracts before purchasing.
Cost and Budget Considerations
Total Cost of Ownership
Evaluate both upfront and long-term costs.
Key Considerations:
Purchase Price: Hydraulic ($5,000-$100,000); servo ($50,000-$500,000).
Operational Costs: Energy (servo lower), maintenance (hydraulic higher), and labor.
ROI: Servo models offer faster ROI for high-precision tasks due to efficiency gains.
Tip: Compare quotes from multiple suppliers to optimize costs.
Budget Control
Align your choice with financial constraints.
Key Considerations:
Refurbished Machines: Certified pre-owned press brakes save 20–40% (The Fabricator).
Financing Options: Leasing or payment plans ease budget constraints.
Tip: Prioritize features matching your production volume and precision needs.
Case Study: Precision Manufacturing with a Servo Press Brake
A mid-sized automotive parts manufacturer in Ohio upgraded from a hydraulic to a servo press brake (Amada HG series) in 2024. Facing demands for ±0.02 mm precision in aluminum panels, the servo model reduced setup times by 30% and energy costs by 40%, per Amada’s performance data. The CNC system’s 3D programming allowed rapid prototyping, increasing throughput by 25%. This case highlights servo press brakes’ advantages for precision-driven, high-volume production.
Emerging Trends in Press Brakes
Industry 4.0 Integration: Smart press brakes with IoT (e.g., Bystronic’s Xpert Pro) offer real-time monitoring, predictive maintenance, and data analytics, improving efficiency by 15–20% (Bystronic data).
Hybrid Models: Combining hydraulic power with servo precision, hybrid press brakes balance cost and performance for medium-scale shops.
Sustainability: Servo models align with green manufacturing by reducing energy use and hydraulic waste.
FAQs: Common Questions About Sheet Metal Press Brakes
Q: Can hydraulic press brakes handle thin sheets?
A: Yes, with proper tooling and pressure adjustments, hydraulic brakes can bend sheets as thin as 0.5 mm, though servo models offer better precision for thin materials.
Q: How do I choose between hydraulic and servo for small shops?
A: Hydraulic models are more cost-effective for small shops with varied bending needs; servo models suit precision-focused tasks but require higher investment.
Q: What maintenance is critical for press brakes?
A: Hydraulic models need regular oil and filter changes; servo models require lubrication and software updates to maintain performance.
Q: How do I ensure consistent bend quality?
A: Use CNC systems with back gauges and verify mold alignment; regular calibration ensures repeatability.
Conclusion
Choosing the right sheet metal press brake involves weighing hydraulic vs. servo models based on your project needs—material thickness, precision, and production volume. Hydraulic press brakes offer cost-effective power for thick sheets, while servo models excel in precision and energy efficiency for high-tech applications. Consider worktable size, mold compatibility, control systems, maintenance, and manufacturer support to ensure a smart investment. With trends like IoT and hybrid models shaping the future, selecting a press brake that aligns with your goals will boost productivity and quality.
Jane Smith
Metalworking specialist with 12 years of experience in sheet metal fabrication and press brake applications, certified by ASME.