CAMT Software Support
Empowering Precision with Cutting-Edge Software Solutions
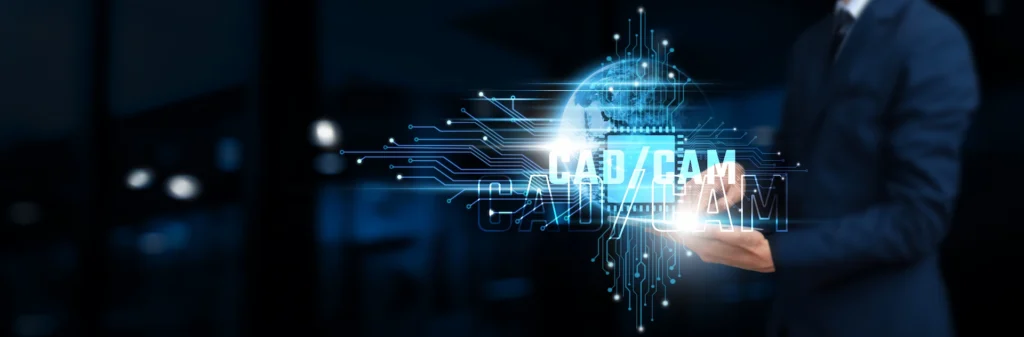
CAMT is committed to delivering world-class software services for bending machines and shears, empowering customers with advanced CAD/CAM solutions, remote support, continuous updates, and customized training. Our software services not only optimize equipment performance but also provide a seamless digital experience through Industry 4.0 technologies and a global support network, addressing diverse production needs.
Core Software Services Summary
- Advanced CAD/CAM Support:
- Offers offline programming and 3D simulation tools (e.g., CAMT Profile-T3D or equivalent), supporting multiple 3D file formats (IGES, STEP, etc.) for precise programming and collision detection.
- Real-time CNC control systems (compatible with DELEM, Cybelec, etc.) streamline bending and shearing processes, reducing setup time and boosting efficiency.
- Remote Support and Rapid Response:
- 24/7 technical hotline and remote diagnostics via high-speed internet resolve software issues quickly, minimizing downtime.
- Global service network with localized support ensures rapid response and regional adaptation.
- Software Maintenance and Updates:
- Regular software updates enhance processing accuracy, speed, and material efficiency.
- Ensures version compatibility and supports customized feature extensions for specialized bending or shearing processes.
- Training and Knowledge Empowerment:
- Provides online and on-site training on CNC systems and offline programming, with multi-language materials.
- Organizes expert workshops to share best practices and industry trends.
2. Expanded Software Service Features
To further elevate the value of CAMT’s software services, we have introduced the following advanced features and services to meet future manufacturing trends and diverse customer needs:
- Customized APIs and Third-Party Integration:
- Provides flexible API interfaces for seamless integration with existing ERP, MES, or CAD/CAM systems.
- Custom development services cater to specific industry needs, such as aerospace, automotive, or construction applications.
- Green Manufacturing Support:
- Optimizes software algorithms to reduce material waste and energy consumption, supporting sustainable production goals.
- Offers energy consumption monitoring with detailed reports to help clients comply with environmental regulations.
- Multi-Device Management:
- Develops a unified management platform for centralized programming, monitoring, and maintenance of multiple CAMT bending machines and shears.
- Enables collaborative operation between machines, optimizing production scheduling and factory efficiency.
3. Value-Added Services
- Subscription-Based Service Model:
- Introduces flexible software support subscription plans (e.g., Basic, Advanced, Custom), offering varying levels of features and support tailored to customer needs.
- Subscribers receive priority updates, dedicated technical support, and customized feature development.
- Data Analytics and Consulting Services:
- Provides production data analytics to generate optimization recommendations, improving efficiency and quality.
- Offers periodic consulting to help clients develop digital transformation strategies aligned with Industry 4.0.
- Global Spare Parts and Software Integration:
- Combines software support with an intelligent spare parts management system, monitoring consumables (e.g., lenses, molds) and recommending procurement plans.
- Collaborates with global supply chains to ensure rapid spare parts delivery, minimizing downtime.
- Community and Knowledge-Sharing Platform:
- Establishes a CAMT user community for online sharing of software tips, case studies, and industry trends.
- Offers free introductory online courses to attract new customers and enhance existing users’ skills.
4. Customer Benefits
- Efficient Production: Intelligent programming and optimization algorithms significantly reduce production cycles and improve accuracy.
- Cost Reduction: Minimizes material waste, energy use, and maintenance costs, optimizing overall operational expenses.
- Flexible Scalability: Custom features and API support meet specific industry and production scale requirements.
- Global Support: 24/7 service and localized support ensure rapid response and issue resolution.
- Technological Leadership: Continuous updates and innovative features keep clients competitive in fast-evolving markets.
CAMT’s software services empower your bending machines and shears with intelligent, reliable, and future-ready solutions, helping you excel in the global sheet metal processing industry. Contact us today to unlock the full potential of your CAMT equipment!
Do you want more specific information? We’ll reach to you as soon as we can
Our Services
- Technical Support
- Maintenance
- Spare Parts
- Trainings
- Software Support
- Warranty Extensions