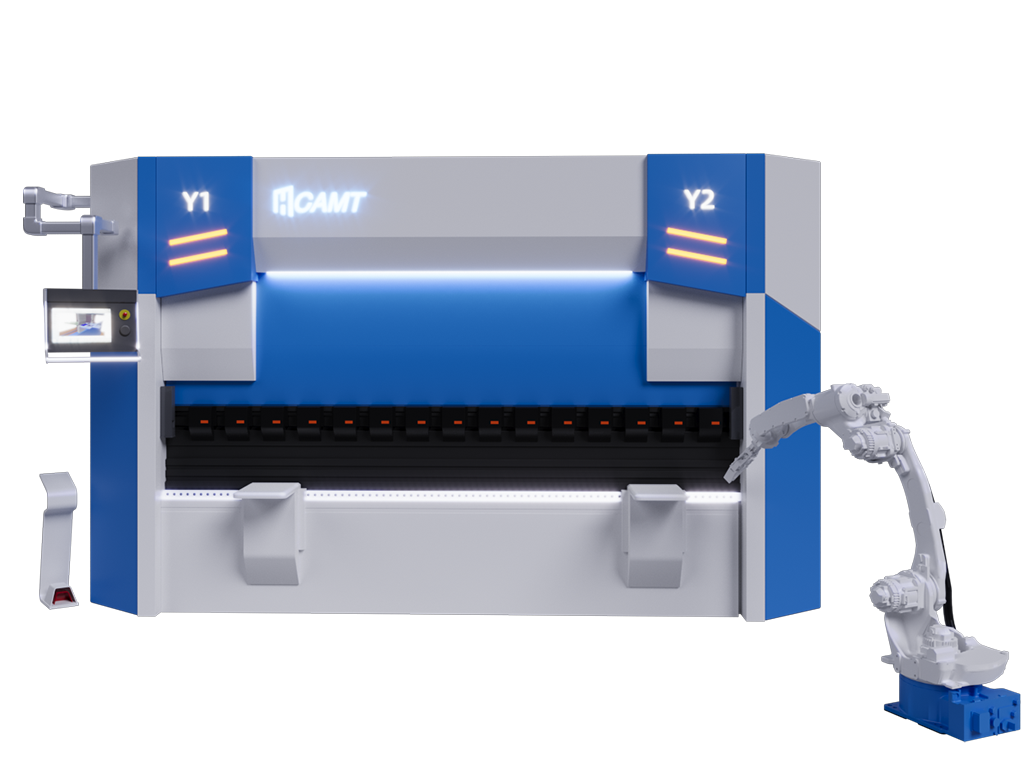
CAMT Fully Automatic Hybrid Press Brake
Apex Press Brake Advanced 6-8 Axis
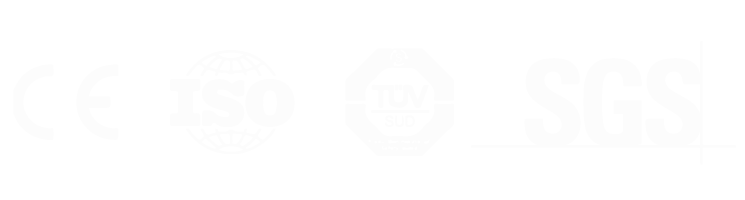
CAMT
Apex Hybrid Press Brake Advanced 6-8 Axis
Fully Automatic Hybrid Press Brake
CAMT 8-axis CNC press brake offers superior precision, flexibility, and efficiency in metal bending operations. The additional axes enable complex, multi-angle bends with high accuracy, reducing setup times and minimizing material waste. Its advanced control system allows for seamless programming and automation, enhancing productivity and consistency across diverse workpieces. The machine’s versatility accommodates a wide range of materials and thicknesses, making it ideal for intricate designs and high-volume production, ultimately lowering operational costs and improving turnaround times.
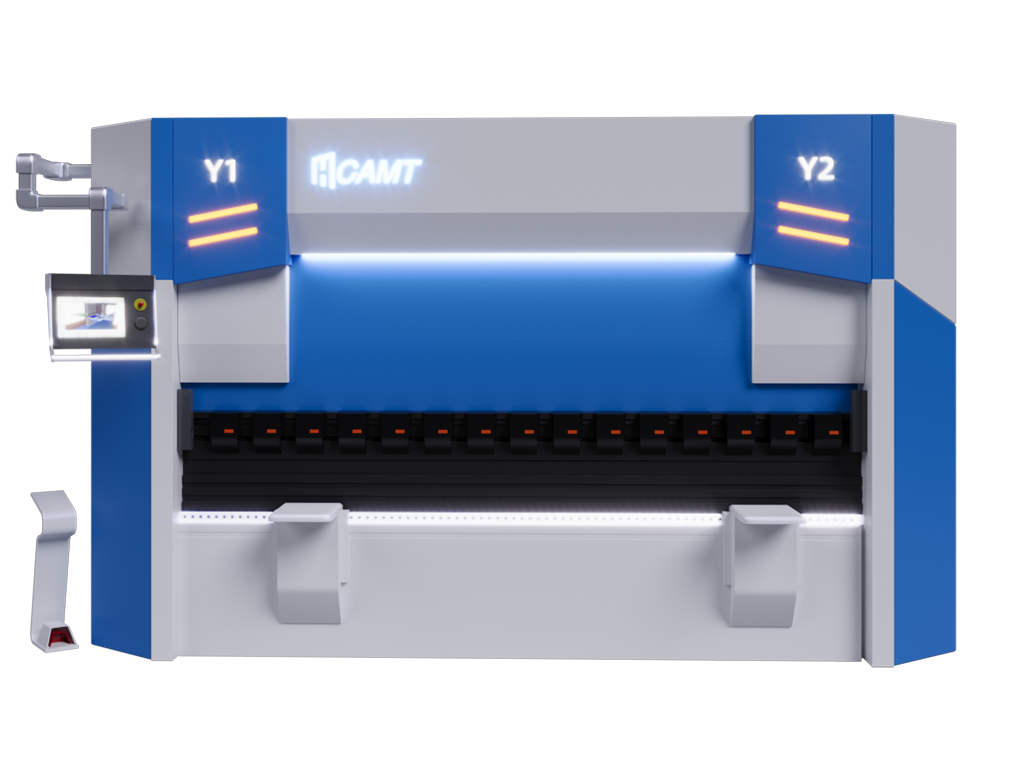
Add Your Tooltip Text Here
Add Your Tooltip Text Here
Less Waste, Less Maintenance Costs
High Performances
Same Job, 50% Less Energy
High Dynamic Y-axis Control
Popular Configuration
- Taiwan TECHMATION SCS920 Automatically for 8+1 Axis
- CHTR Rear BGA 600MM with 300MM/S & X1/X2, R1/R2-Axis, Z1/Z2-Axis as Standard
- CAMT Itergral Advanced Hybrid Servo System
- 4 V Double CNC die series &835mm punches
- High Precision & Multi Point Mechanical Crowning
- Imported Italy GIVI Maganetic Misure
- Italy DSP Laser Protection-TOP
- Germany BOSCH-REXROTH Proportional Valve
- Full ESTUN Servo Motor/Drive
- Graphite Self-lubricating Copper Plate
- Safety France Schneider Electric System Components
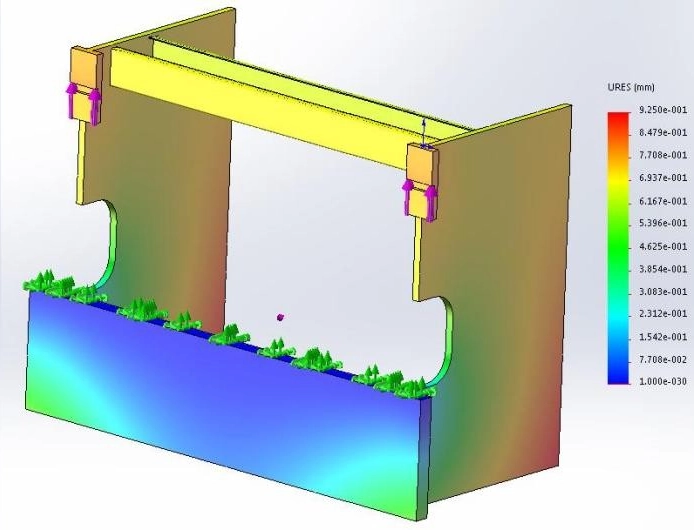
FEA & Stress Analysis of Press Brake
Stress Analysis & Finite Element Analysis
CAMT FEA plays a pivotal role by optimizing structures through stress distribution analysis to identify and reinforce high-stress areas, enhancing strength while minimizing material waste; verifying performance by predicting deformation under extreme loads (e.g., 600 tons) to ensure precision and stability for Y1/Y2 synchronization; assessing safety by evaluating stress concentration to mitigate fatigue or fracture risks for long-term reliability; and conducting dynamic analysis to simulate transient loads and vibrations in complex scenarios like tandem bending or high-speed operations, optimizing servo motor response and overall machine stability.
Taiwan TECHMATION Advanced Automatically SCS920
SCS920 Controller: Efficient and Intelligent Industrial Solution
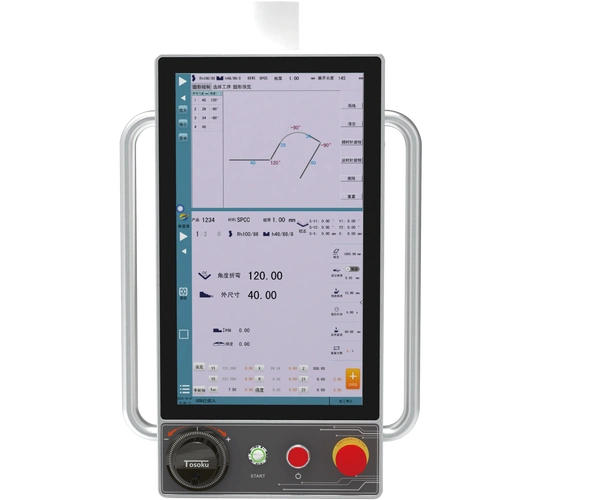
DELEM CNC Control System for Bending Solution
DELEM DA69T Touch 3D Graphical Control
The DELEM DA-69T offers 2D as well as 3D programming that includes automatic bend sequence calculation and collision detection. Full 3D machine set-up with multiple tool stations giving true feedback on the product feasibility and handling.
- 17" high resolution colour TFT
- 2D and 3D graphical touch screen programming mode
- 3D visualisation in simulation and production
- Full Windows application suite
- Delem Modusys compatibility (module scalability and adaptivity)
- USB, peripheral interfacing
- Profile-T2D offline software
- Sensor bending & correction interface
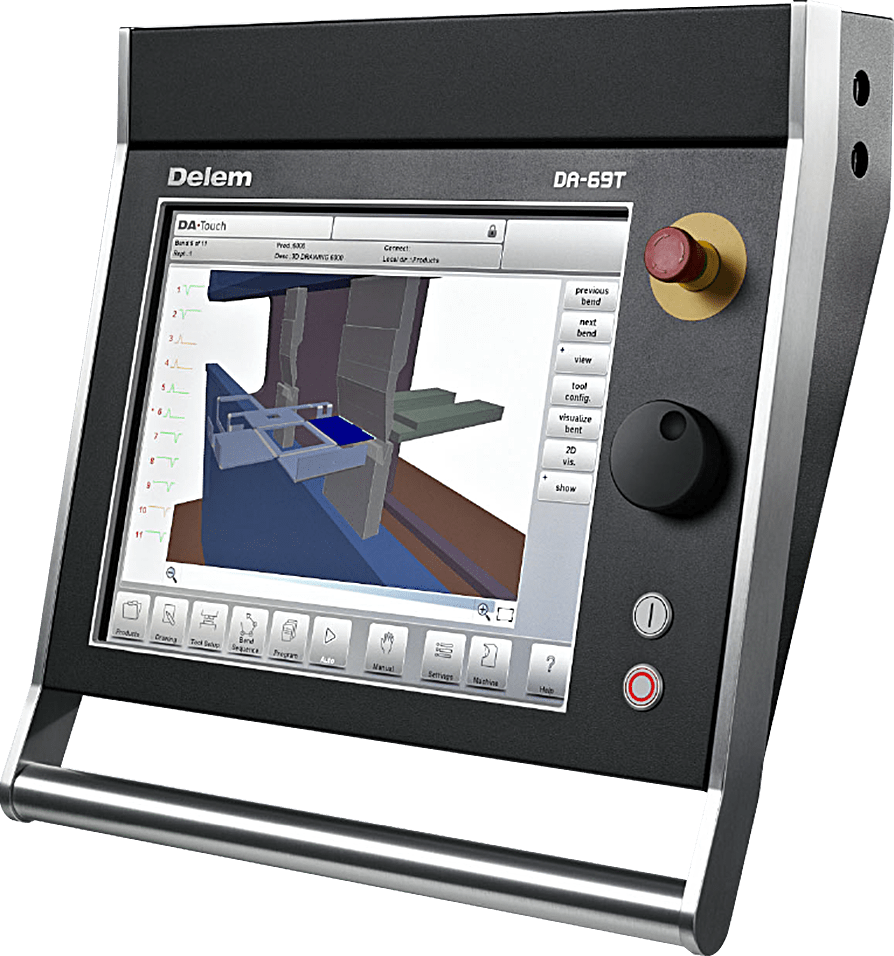
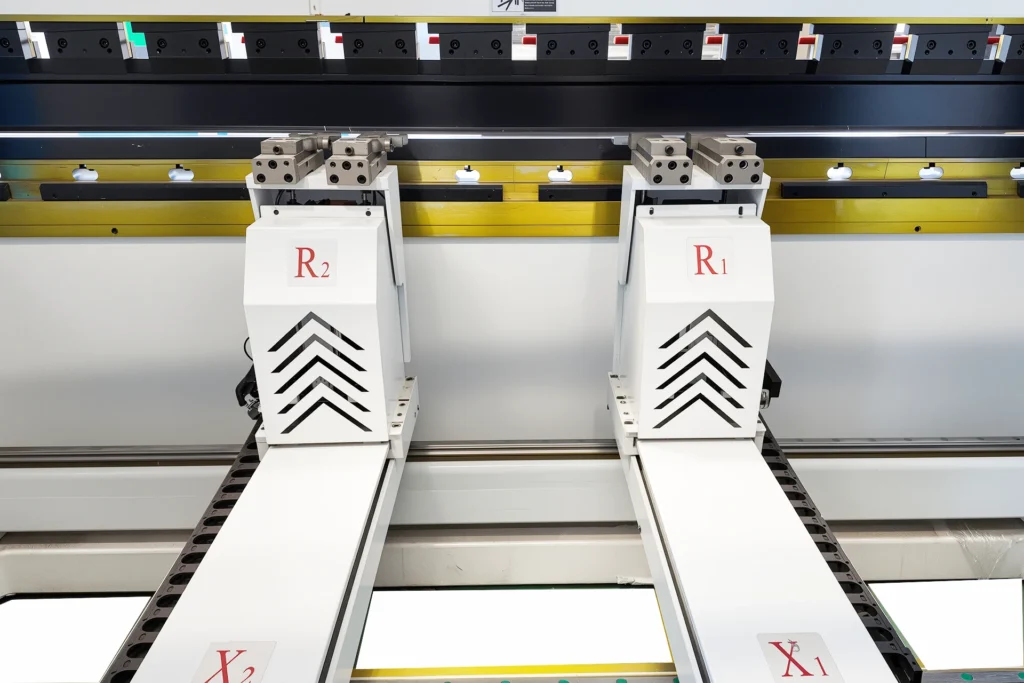
CAMT Advanced Automatically BGA 8 Axis
CHTR Advanced 8-Axis CNC BackGauge System
- Achieves ±0.03 mm mechanical accuracy with ball screws, linear guides, and stable racks, ensuring precise positioning and stability during bending.
- Z1-Z2 axes operate at 600 mm/s, and X1-X2, R1-R2 axes at 300 mm/s, boosting productivity for high-intensity tasks.
- Features smart fingers with double-stop and micrometric adjustment, allowing precise modifications for complex bending requirements.
- Supports 8 axes (X1, X2, R1, R2, Z1, Z2, and two additional axes), with X1-X2 backgauges capable of independent operation, offering enhanced flexibility and a wider processing range for diverse workpieces.
- Built with high-quality transmission components, ensuring long-term reliability and reduced maintenance costs.
- Ideal choice for modern press brake operations with intelligent automation and real-time diagnostics.
Most Advanced BackGauge System
Precision 8+1 Axis BGA System with Dual-Zone Functionality
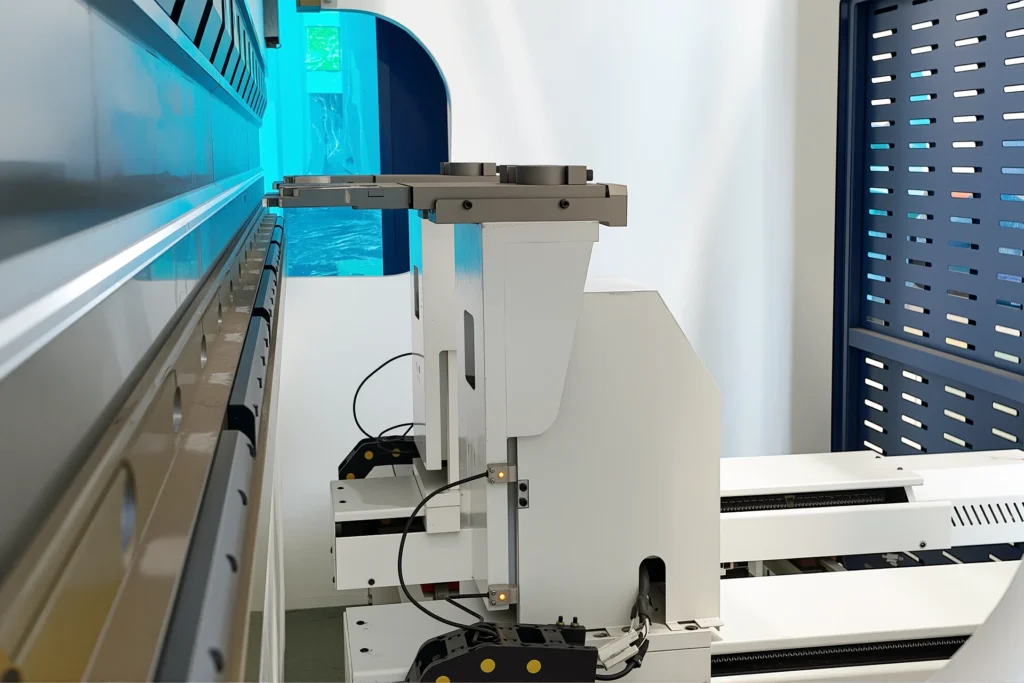
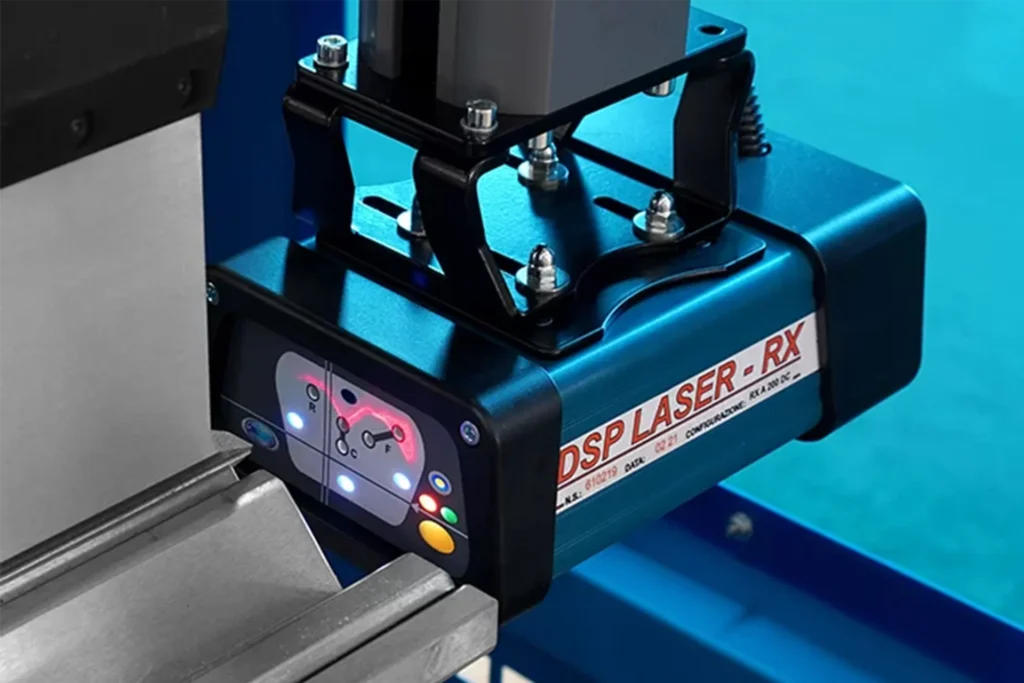
DSP Laser Safety Protection - Optional
CAMT® CNC press brake optional DSP thateliminating risks caused by the rapid movement of the machine’s slide. It creates a block-shaped protective zone.The protective zone is fixed below the tool tip and moves synchronously with the mold, ensuring that any object below the mold during high-speed descent enters the DSP-generated protective zone before contacting the tool tip.
Advantages:
- Class 1M block laser emitter
- Safety rating up to CAT.4 and SIL3
- System response time of 5ms
Mechanic Compensation
Precise Effectiveness & Muti-Point Crowning of Press Brake Machine
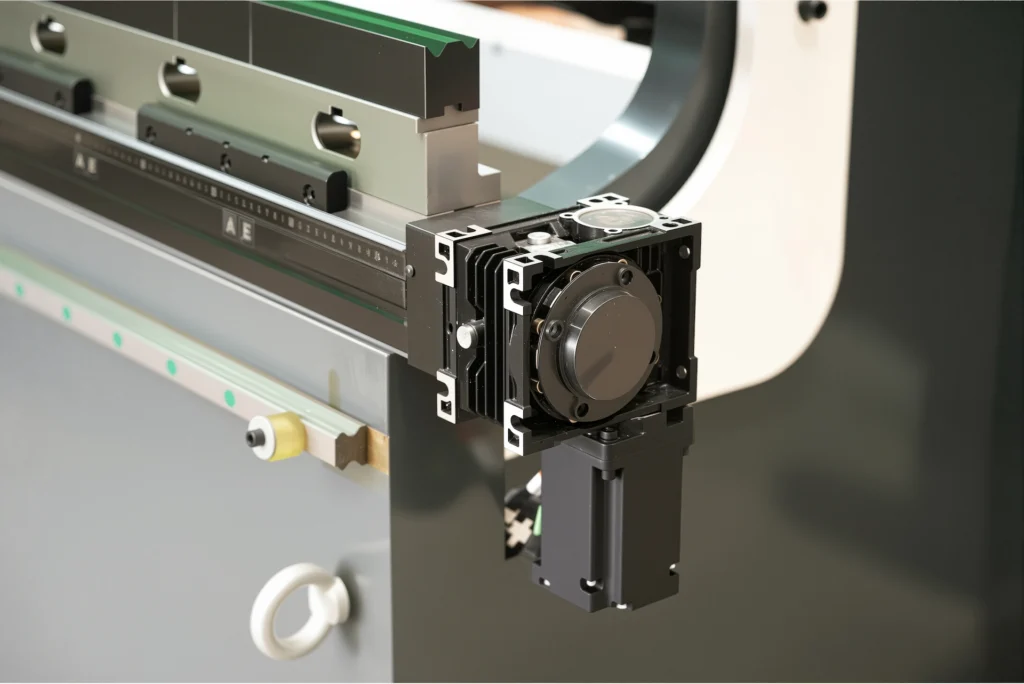
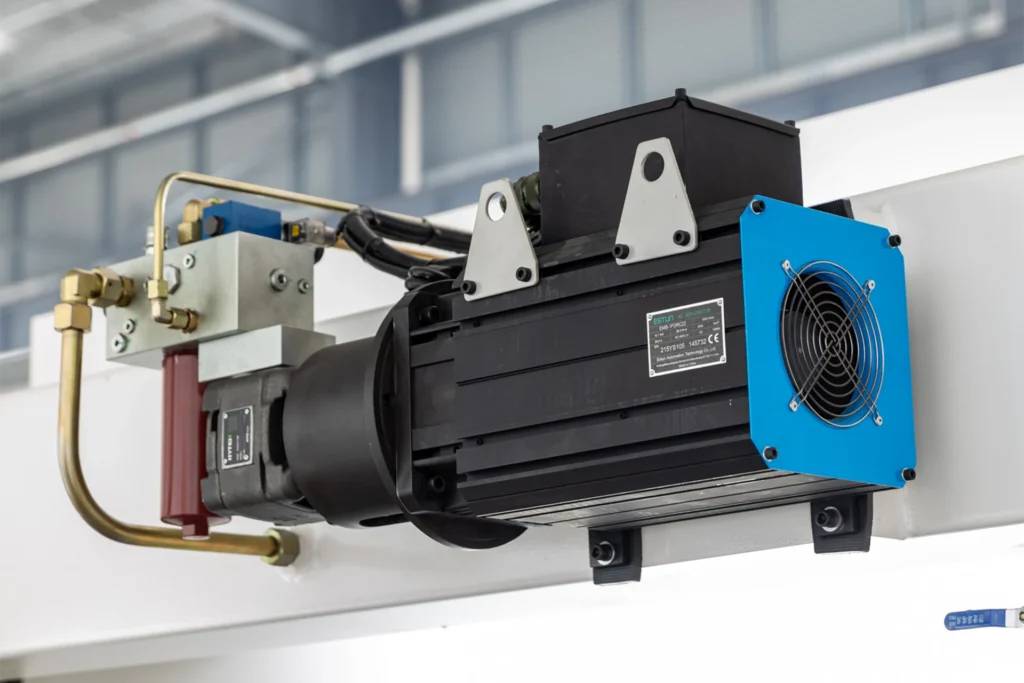
Fully ESTUN FULL SERVO/DRIVE System for Hydraulic Press Brake
Advantage:
- Precise Motion Control
- Dynamic Response
- Energy Management
- High Precision and Stability
- Fast Response
- Energy Efficiency &Easy Integration
Germany BOSCH-REXROTH Hydraulic System
CAMT Party with Top-Tier Closed- Loop Control Bending Technology
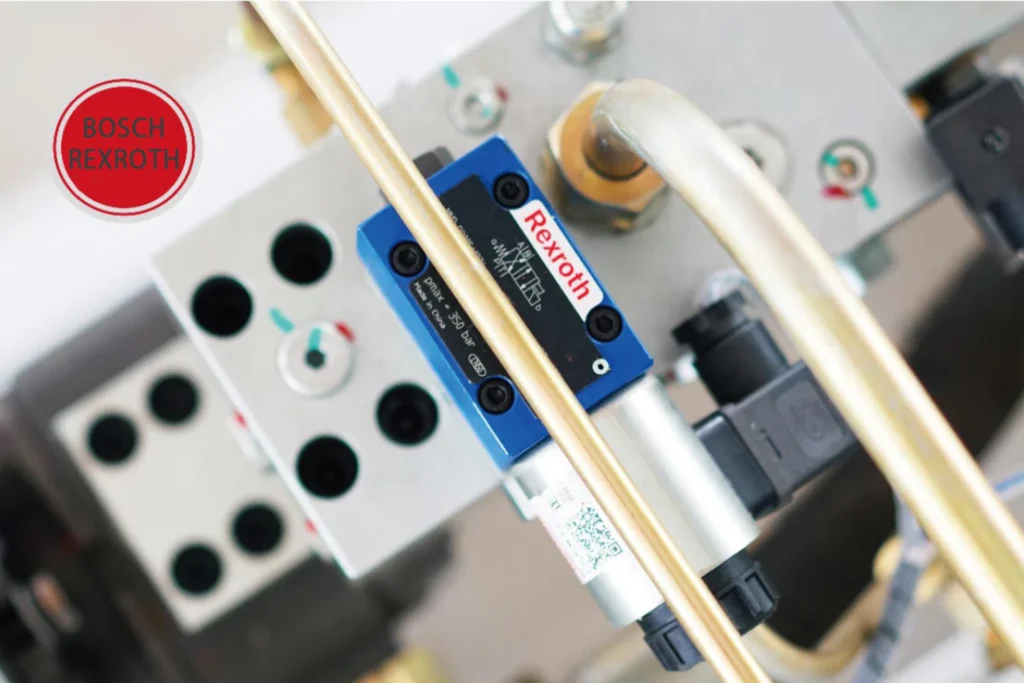
Advantage:
- Ensures press brake machine stability and rigidity with strict inspections and finite element analysis.
- Delivers real-time feedback and micron-level precision.
- Boosts efficiency with 20% faster response than hydraulic systems.
- Eco-friendly design with regenerative power recovery.
- Advanced technology for superior performance.
- Automatic angle correction and collision prevention.
- Backed by professional engineers for lifelong assurance.
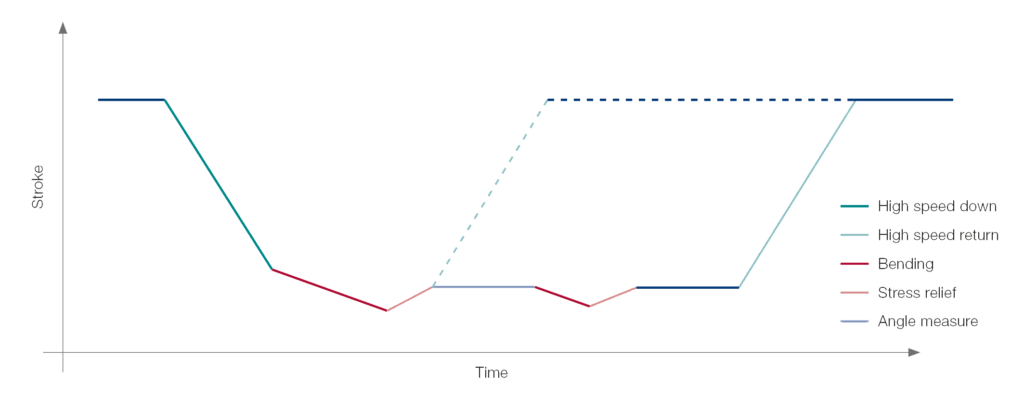
Bending Offline Programming Software
The Core Solution for Maximizing Sheet Metal Processing Efficiency
The DELEM DA Series Offline Programming Software significantly enhances press brake productivity and processing capacity through intelligent technology. The integrated Profile-T3D system delivers a complete offline programming environment with 3D bending process simulation capabilities.
Key Technical Advantages of Profile-T3D:
As an indispensable intelligent tool for modern sheet metal fabrication, Profile-T3D provides three core benefits: Rapid import and automatic unfolding of 3D engineering drawings; intelligent optimization of tool configuration and bending sequences; and advanced 3D dynamic simulation to preemptively detect collision risks, ensuring safe and reliable processing.
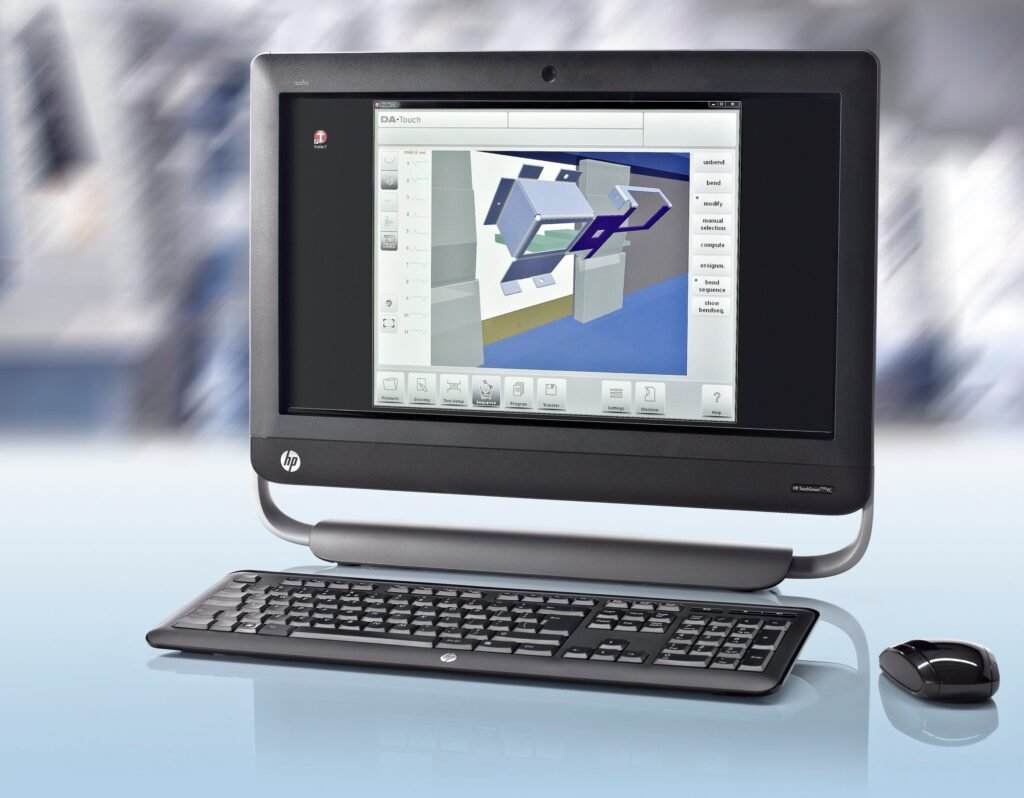
The Next-Gen Smart Manufacturing Automation Solution
Leverages the CAMT® intelligent control hub and Industrial IoT (IIoT) platform to achieve high-efficiency connectivity between devices, systems, and the cloud, creating a truly seamless digital production environment. With multi-protocol compatibility, plug-and-play interfaces, and cross-platform collaboration, it significantly enhances programming efficiency, data acquisition completeness, and remote response speed. Featuring standardized connectivity, secure data transmission, and flexible scalability, it has already helped hundreds of enterprises reduce integration costs and accelerate smart manufacturing transformation. Whether for CAD/CAM integration, real-time monitoring, or cloud collaboration, this solution provides reliable technological support to modern factories, making automated production smarter and more efficient.
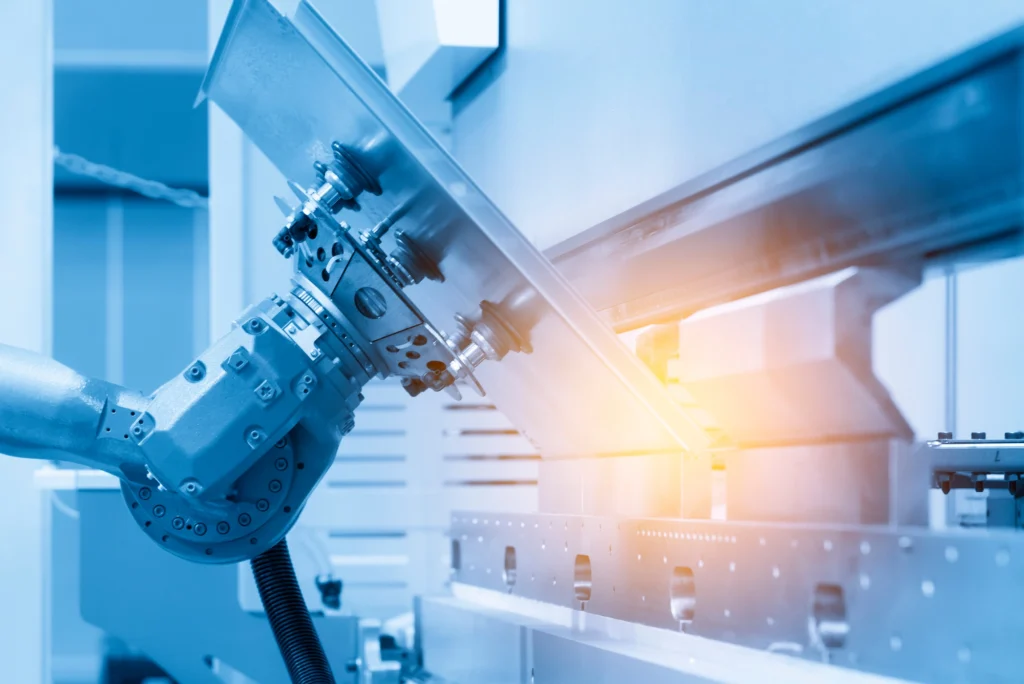
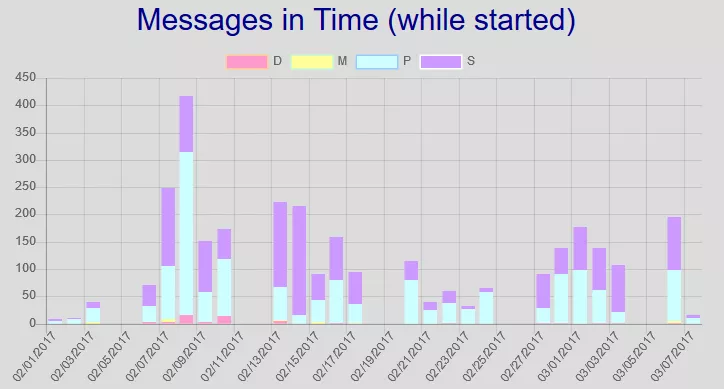
Runtime Message Monitoring
This bar chart displays statistics of various message types triggered during DA-Control operation. Only messages that were active during system runtime are recorded, including the following categories:
- D - Delem system application messages
- M - DM module messages
- P - Safety PLC generated messages
- S - Sequencer messages
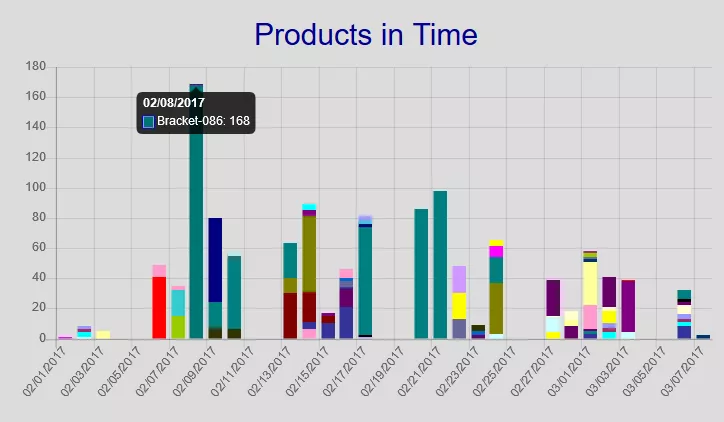
Product Production Timeline
This block presents daily production quantities for each product via bar charts. Hovering over any bar will display the product ID and specific production quantity for that date.