The most effective method for handling large sheets during bending
Bending Follower Supports
The optimal approach for managing large sheets during bending involves using CAMT's innovative press brake electric sheet metal follower lifters, fully controlled by CNC. These motorized sheet followers, featuring a dual interpolated axis configuration, provide continuous support to the sheet throughout the bending process, minimizing scratches and counterbends while streamlining operator tasks.
Front Sheet Follower Supports System
The hydraulic press brakes with Sheet supports follower system can be added to various large-scale machine materials, greatly simplifying the workload of machine material exploration workers, improving bending efficiency, and simplifying operations.Independent series machine control system, capable of initiating machine operations in sync with the bending process, achieving 100% synchronization with the bending steps.
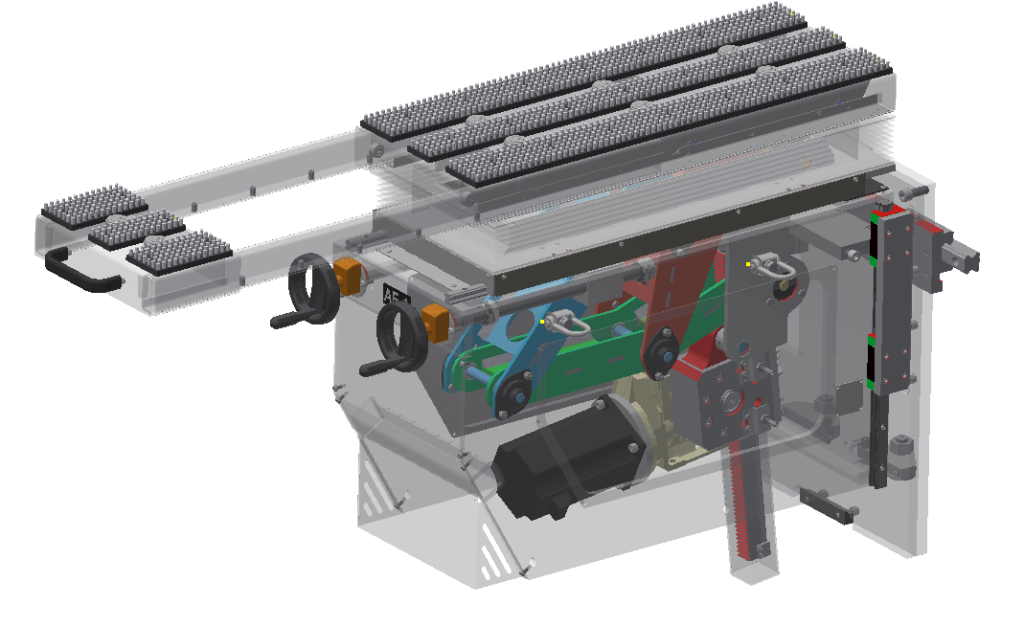
Automatically support the sheet metal, eliminating manual intervention and preventing sagging or misalignment during bending. It ensures consistent bend angles, protects the material surface from scratches, and is particularly suitable for long sheets, thin plates, and high-precision bending processes, significantly improving processing efficiency and quality stability.
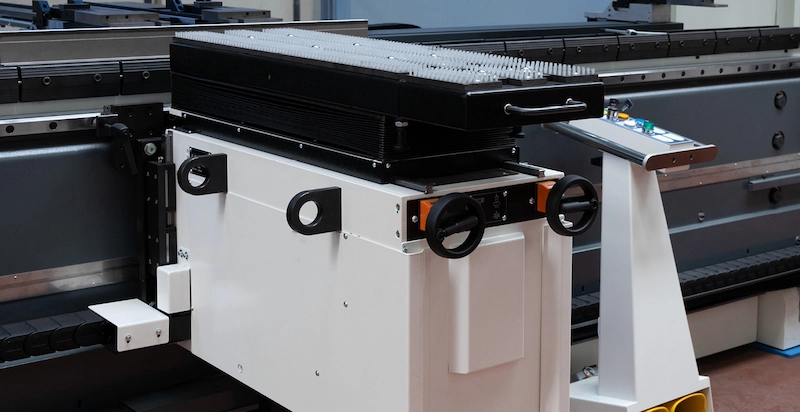
Press brake front support follow-up system of a press brake utilizes servo or hydraulic control to synchronize the support mechanism with the ram movement. Equipped with sensors, it dynamically adjusts the support height in real time to maintain contact with the sheet metal without applying pressure, compensating for gravity-induced sagging or deformation to ensure precise follow-up support during bending.
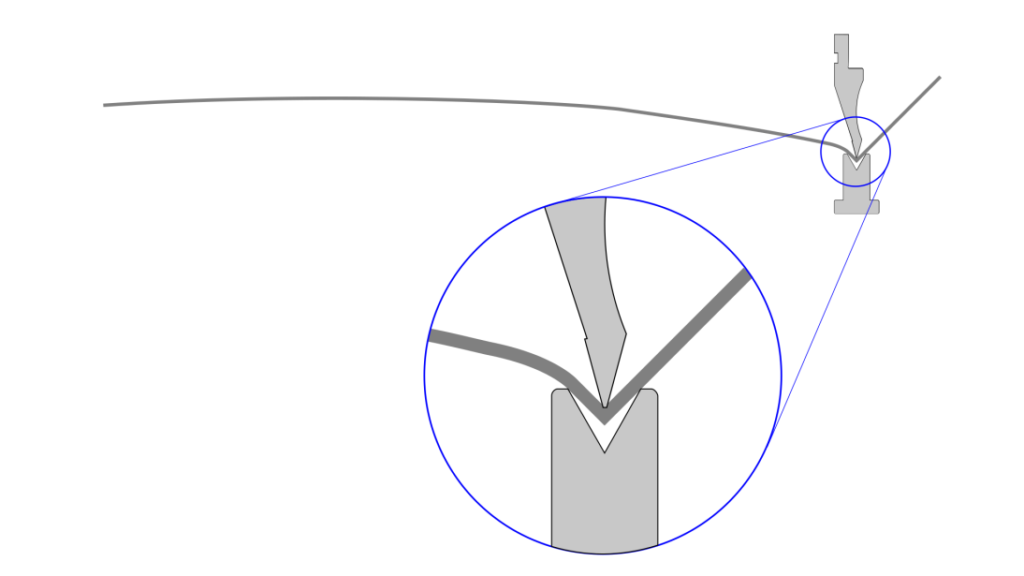
Advantage:
- Equipped with a parking position to avoid interference with the workpiece during reverse bending.
- Flexible and easy to use, with quick installation and removal, allowing it to be transferred and mounted on another machine.
- Equipped with a brush table to prevent sheet scratching, slipping, or falling.
- Reducing the operator's workload in handling heavy materials, improving bending efficiency, and minimizing operator risk.
- Independent modular control system ensures perfect 100% synchronization with the Y-axis during the bending process.
- Automatically adjusts vertical and horizontal positioning based on die height and V-opening size.