Production Advantages
R&D And Processes

Mechanical Engineering Design
CAMT has strong in-house R&D capabilities and extensive experience in designing high-precision components using SOLIDWORKS 3D CAD modeling. Our engineers employ first-principles calculations to optimize the structural design of CNC press brakes and laser cutting machines.
All independently developed designs and technical drawings incorporate advanced ergonomic principles to maximize operator comfort and work efficiency.
The application of computer-aided engineering (CAE) for heavy industrial equipment represents an innovative technological approach, positioning traditional manufacturers at the forefront of Industry 4.0 implementation.
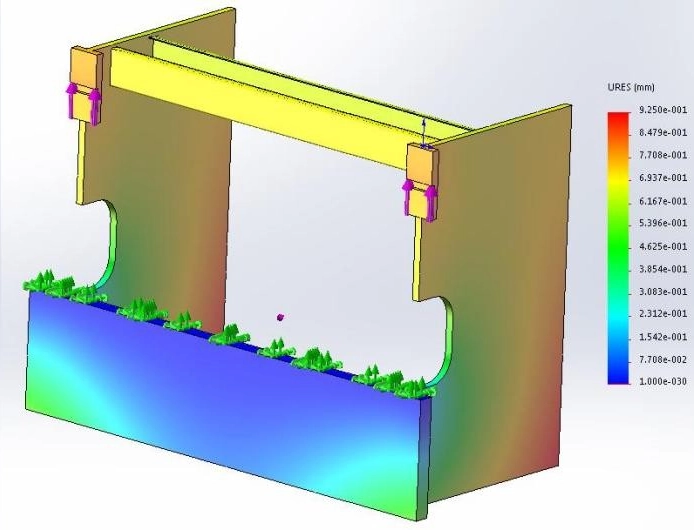
FEA & Stress Analysis
FEA accurately predicts stress distribution patterns, deformation characteristics, and load-bearing capacities under various operating conditions. This advanced analytical approach enables engineers to identify and reinforce potential weak points in the frame, ram, and bed assembly while optimizing material usage through topology optimization techniques. The analysis specifically targets critical performance factors including ram deflection compensation accuracy, structural vibration damping, and fatigue resistance under cyclic loading conditions. Through iterative simulation processes, FEA facilitates the development of press brakes with enhanced rigidity-to-weight ratios, improved energy efficiency, and prolonged service life.
Finite Element Analysis (FEA) provides crucial advantages for press brake slide design by enabling precise stress mapping, deformation prediction, and dynamic performance optimization. The analysis identifies high-stress concentrations, calculates deflection compensation needs, and validates fatigue resistance – allowing engineers to optimize slide geometry for maximum stiffness-to-weight ratio.


Heat Treatment Processes
Stress-relief tempering treatment for machine tool frames involves controlled heating (typically 550-650°C) followed by gradual cooling to reorganize the metallic microstructure and eliminate residual stresses from casting/welding processes. This thermal treatment enhances the frame’s structural integrity by achieving three critical improvements: 80-95% reduction in internal stresses that could cause dimensional instability. 20-30% increase in vibration damping capacity through grain refinement. Improved load distribution characteristics. The treated frame demonstrates measurable performance enhancements including 0.005mm/m better geometric accuracy under load, 15-20% higher static/dynamic stiffness, and 50% longer service life against fatigue cracks. These metallurgical improvements directly translate to superior machine tool performance: reduced chatter during heavy cuts, maintained positioning accuracy over extended periods, and minimized need for recalibration – particularly critical for high-precision CNC equipment operating under variable thermal and mechanical loads.
Mechanical Processes
Full machining of machine tool frames on floor-type boring mills provides critical advantages for heavy-duty equipment by achieving unmatched structural precision and performance characteristics. This comprehensive machining process ensures all critical mounting surfaces (guideways, spindle interfaces, and column mating faces) are finished in a single setup with positioning accuracy within 0.01mm/m, eliminating cumulative errors from multiple clamping operations. The key benefits include: perfect geometric alignment of all functional surfaces (flatness ≤0.005mm/1000mm). Optimized stress distribution through uniform material removal. Superior surface finish (Ra 0.8-1.6μm) for enhanced component mating and wear resistance. These precision-machined frames demonstrate 30-40% better load distribution compared to conventionally manufactured bases, resulting in 20% higher dynamic stiffness and 50% longer guideway service life. The process particularly benefits large CNC boring/milling machines by ensuring thermal stability during heavy cutting operations (maintaining ≤0.015mm dimensional variation under 30°C temperature fluctuations) and providing vibration damping characteristics critical for achieving micron-level machining accuracy.
