CAMT Training
Empowering Precision: World-Class Training for CAMT Bending & Laser Excellence
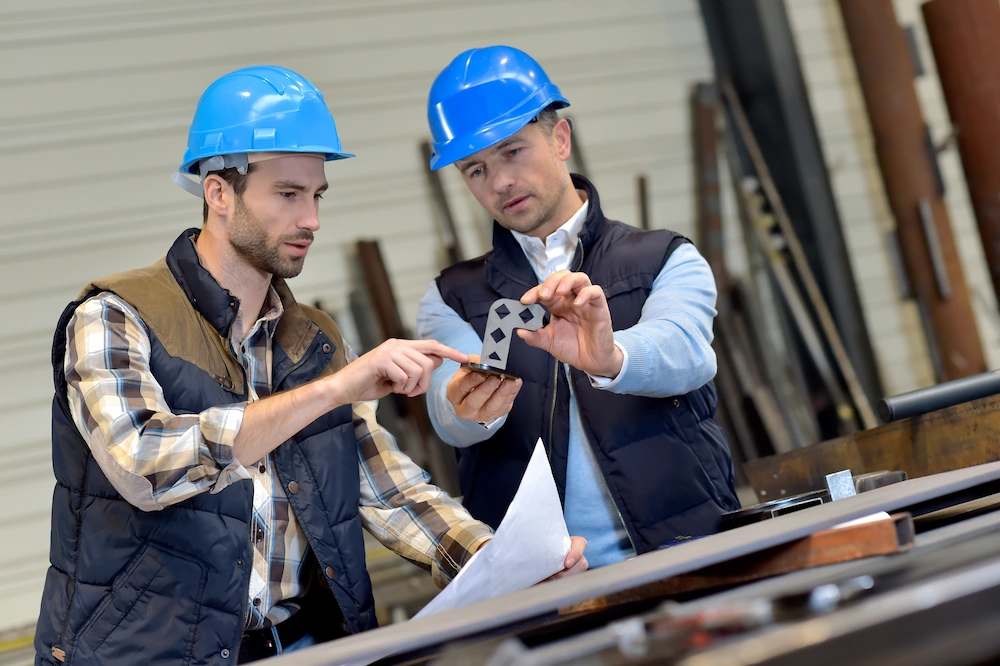
CAMT Bending Machine and Laser Sheet Metal Equipment International Training Services
1. Training Objectives
- Enable international operators to proficiently master the safe operation of CAMT bending machines, laser cutting machines, and other sheet metal equipment.
- Optimize equipment performance, enhance production efficiency, and adapt to local production needs.
- Train maintenance personnel in equipment care, fault diagnosis, and repair skills.
- Ensure compliance with international safety standards (e.g., ISO, CE) and local regulations.
2. Target Audience
- Overseas factory operators
- Equipment maintenance technicians
- Production managers
- Safety and compliance officers
3. Training Content
(1) Equipment Operation Training
- Equipment Fundamentals:
- Overview of the structure, working principles, and key components of CAMT bending machines and laser cutting machines.
- Operation of CNC control systems or laser cutting software (with multi-language interface support).
- Sheet metal processing basics, including material properties, bending angle calculations, and laser cutting parameter settings.
- Operational Procedures:
- Standardized startup and shutdown processes.
- Bending machine mold selection, installation, and calibration.
- Laser cutting machine focus adjustment, gas management, and cutting parameter optimization.
- Program editing and import (G-code or proprietary software).
- Hands-On Training:
- Practical exercises for processing locally common materials (e.g., stainless steel, aluminum, galvanized sheets).
- Programming and processing of complex parts (e.g., 3D bending, precision cutting).
- Solutions for common issues, such as bending angle deviations or laser cutting edge quality.
(2) Equipment Maintenance Training
- Daily Maintenance:
- Cleaning and lubrication: bending machine sliders, guide rails; laser machine lenses, and optical paths.
- Routine inspections: electrical systems, hydraulic systems, and gas circuits.
- Consumable management: laser nozzles, lenses, and bending machine molds replacement cycles.
- Troubleshooting:
- Diagnosing common issues, such as reduced bending accuracy or poor laser cutting quality.
- Interpreting error codes and implementing localized solutions.
- Digital maintenance record management.
- Preventive Maintenance:
- Developing maintenance plans suited to local conditions (e.g., high temperature, humidity).
- Lifecycle management of critical components and spare parts procurement guidance.
(3) Safety and Compliance Training
- International Safety Standards:
- Compliance with ISO 13849, CE certification, or local safety regulations.
- Laser equipment radiation protection and ventilation requirements.
- Proper use of personal protective equipment (PPE), such as safety goggles and cut-resistant gloves.
- Emergency Response:
- Procedures for handling equipment failures, electrical incidents, or fires.
- Safety Operating Procedures (SOP) training in the local language.
- Safety Awareness:
- Identifying operational risks (e.g., high-pressure hydraulics, laser radiation).
- Cross-cultural safety training tailored to local work practices.
4. Training Delivery Methods
- On-Site Training:
- CAMT-certified engineers travel to the client’s country for hands-on training with actual equipment.
- Localized case studies to address client-specific production challenges.
- Online Training:
- Delivered via video conferencing platforms (e.g., Zoom, Teams) for real-time instruction.
- Multi-language manuals, video tutorials, and virtual simulation software provided.
- Flexible scheduling to accommodate time zone differences.
- Hybrid Training:
- Combines online theoretical courses with on-site practical training.
- Ongoing remote technical support to resolve post-training issues.
- Customized Training:
- Tailored to the client’s regional language, culture, and industry needs.
- Specialized courses for specific equipment models or processing techniques.
5. Training Duration and Schedule
- Basic Training: 2-3 days, covering equipment operation and basic maintenance.
- Advanced Training: 4-5 days, focusing on complex programming, process optimization, and advanced maintenance.
- Periodic Refresher Training: 1-2 days annually, delivered online or on-site to update technical knowledge.
- Flexible Scheduling: Adjusted to client time zones and production schedules.
6. Language Support
- Multi-language training in English, Spanish, French, German, Chinese, and more.
- Professional interpreters or localized trainers ensure seamless communication.
- Training materials (manuals, presentations, videos) available in multiple languages.
7. Training Outcomes
- Certification: Operators who complete training and pass assessments receive CAMT international certification.
- Training Materials: Multi-language operation and maintenance manuals (digital or print).
- Ongoing Support:
- 24/7 global technical support hotline.
- Periodic remote follow-ups to address equipment usage issues.
- Guidance on spare parts procurement and localized supply chain solutions.
8. Training Advantages
- Global Reach: CAMT’s training network spans multiple countries for rapid response.
- Localized Adaptation: Training content tailored to local materials, climate, and industry standards.
- Expert Team: Delivered by CAMT-certified engineers or regionally authorized trainers.
- Continuous Updates: Training content updated with the latest equipment technology and industry trends.
9. Logistics and Support
- Visa and Travel: Assistance with visa applications and travel arrangements for trainers.
- Equipment Support: Provision of training-specific spare parts, tools, and simulation equipment.
- Local Partnerships: Collaboration with local distributors or technical service centers to ensure seamless delivery.
Do you want more specific information? We’ll reach to you as soon as we can
Our Services
- Technical Support
- Maintenance
- Spare Parts
- Trainings
- Software Support
- Warranty Extensions