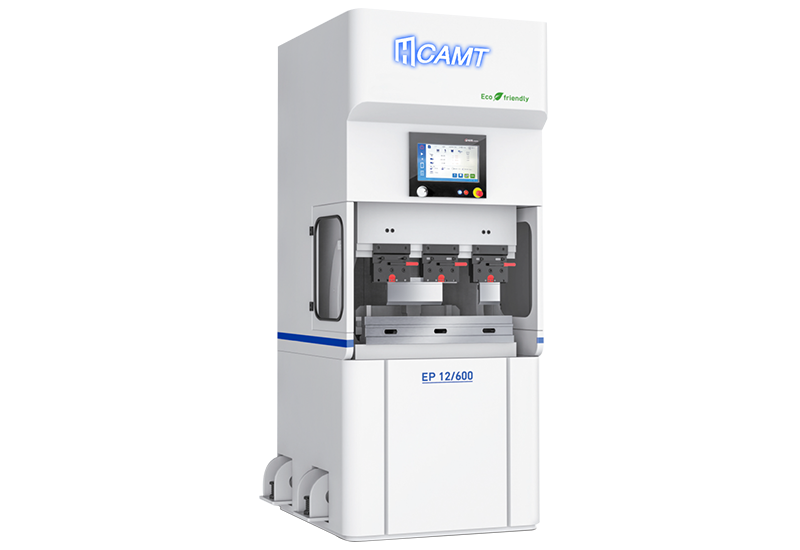
Efficiency Servo Electric Press Brake EPB Series
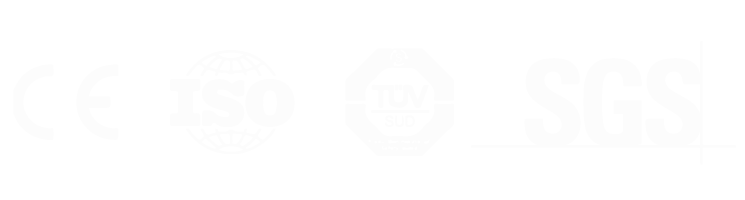
Full Pure Electric Mini Bending Machine for Metalworking
Super Fast -Most Effeciency–Eco Friendly Energy
CAMT full servo electric press brake operates on a sophisticated principle where servo motors, controlled by an advanced CNC system, drive the ram’s movement to execute precise bending tasks, eliminating the need for hydraulic oil used in traditional machines. The CNC system processes programmed parameters such as bending angles and lengths, while real-time sensor feedback ensures exceptional accuracy down to ±0.005mm, making it ideal for intricate metalworking applications. Its advantages are numerous: it offers superior energy efficiency and environmental sustainability by avoiding hydraulic systems, thus reducing energy consumption and eliminating oil-related pollution. The machine also boasts high-speed performance with rapid response times, significantly shortening bending cycles and boosting overall productivity. Maintenance is minimal due to the absence of hydraulic components, which lowers operational costs and enhances equipment longevity. Furthermore, its flexible CNC programming enables seamless transitions between different workpiece specifications, catering to diverse production needs with ease, making it a versatile and cost-effective solution for modern manufacturing.
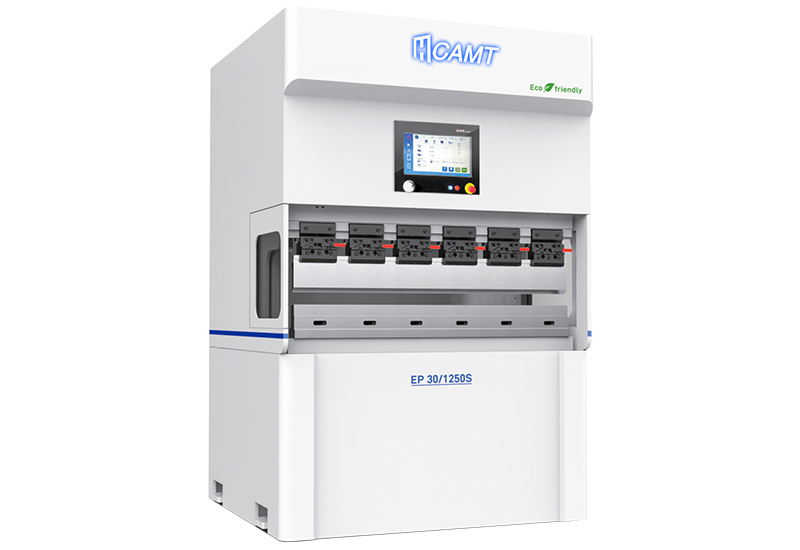
Add Your Tooltip Text Here
Add Your Tooltip Text Here
Stable&Durable
High Precision&Effeciency
Long Service Life Time
Power Saving & Eco-Friendly
Standard Equipment
- 21.6' color high-definition touch screen with friendly human-machine interface
- CHTR Rear BGA 600MM with 300MM/S
- 2 V Double CNC die series &835mm punches
- VICHI Full Servo Motor&Drive
- Imported Italy GIVI Maganetic Misure
- Taiwan Precise HIWIN/TBI Ball Screw & LinearGuide
- Automatic Lubrication Oil System
- Safety France Schneider Electric System Components
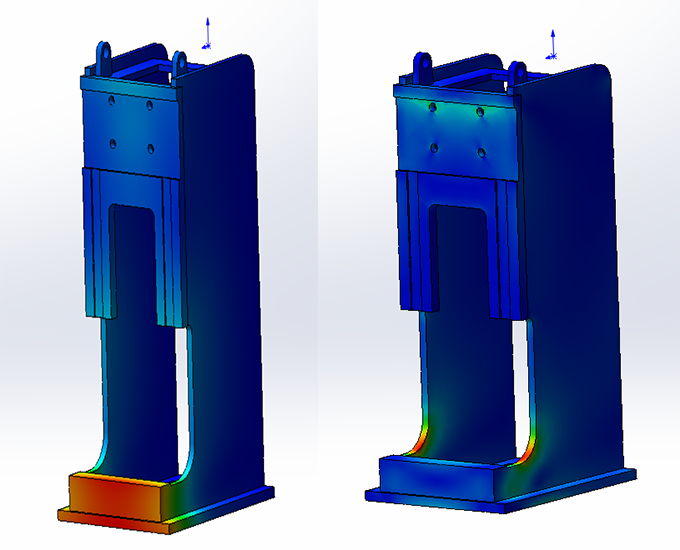
FEA & Stress Analysis of Small Press Brake
Stress Analysis & Finite Element Analysis
CAMT evaluate its structural integrity, performance, and efficiency under operational loads. The analysis focuses on key components, including the frame, bending arm, and drive system, modeled using 3D finite element methods. Material properties, such as steel for the frame and high-strength alloys for moving parts, are defined to ensure accuracy. Boundary conditions simulate real-world loading scenarios, including maximum bending forces and torque from the electric motor. The FEA assesses stress distribution, deformation, and fatigue life to identify potential failure points. Results indicate that the machine’s design meets safety and performance requirements, with optimized stiffness and minimal deflection under load. Recommendations for improving structural efficiency and reducing material usage are provided based on the analysis. This study demonstrates the effectiveness of FEA in enhancing the design and reliability of pure electric bending machines.
Intergral Advanced CNC Control System
More Than 10 Years R&D CNC Control
- 21..6-inch color high-definition touch screen with friendly human-machine interface
- "One-page" programming navigation, one page can display all data, and it isfaster to modify the curve information
- The system supports 4-axis control, meeting the highest control conditions of 4+2 axis bending machine
- The Linux operating platform is stable and reliable, with fast startup speeddand can be directly powered off and shut down
- The bending data is automatically calculated, the bending speed of each step is programmable, the slow down and mid-stop can be controlled, and thehome page has convenient functions such as fast mold alignment, so novicescan quickly get started
- Rich interfaces, can be easily and conveniently connected to the automateddproduction line as a bending unit
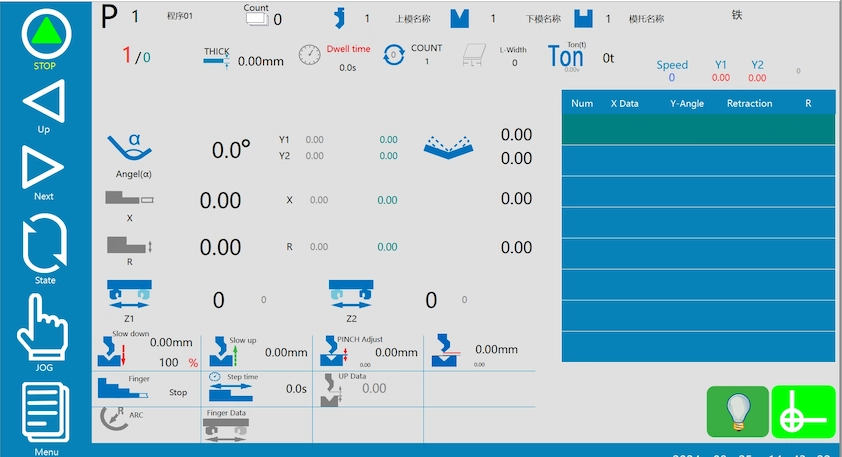
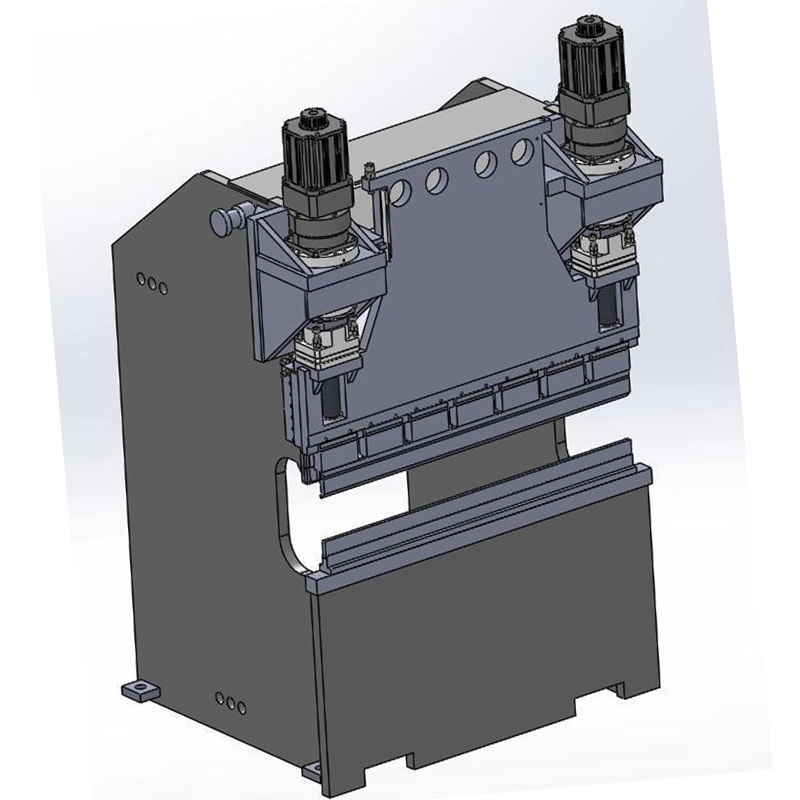
VICHI Servo Drive Theory
Servo Pure Press Brake Direcly Drive-Structure &Principle
Advantages:
The innovative design of a direct-connected all-electric servo press brake integrates a servo motor, reducer, and heavy-duty lead screw in a streamlined configuration, eliminating the synchronous pulley mechanism. This approach resolves issues associated with synchronous pulley systems, such as high noise levels and safety concerns due to belt breakage. The new design offers low noise, minimal repeat positioning error, a simple and reliable structure, and reduced costs.
In this system, the servo motor directly drives the reducer and lead screw, enabling rotational motion. The lead screw nut, driven by the screw’s rotation, moves vertically, actuating the slider. The slider, in turn, drives the upper mold to perform vertical movements, facilitating precise sheet metal bending. This direct-connection mechanism enhances operational efficiency, reliability, and precision while maintaining a cost-effective and compact design, making it an ideal solution for modern sheet metal processing.
Direct-Connect Design
Direct-Connected Main Motor, Reducer, and Lead Screw
- Compared to synchronous belt systems, the direct-connected design is easier to assemble and more reliable
- Unlike synchronous belt systems, the direct-connected configuration eliminates the risk of belt breakage, which can lead to uncontrolled slider movement and braking issues.
- Generates significantly less noise than traditional synchronous belt transmission
- superior accuracy without requiring a magnetic scale for closed-loop control, reducing costs
- his feature counteracts the slider’s gravity, eliminating the need for a brake motor in the servo system, further lowering costs
- The main spindle servo motor operates at 4000 RPM, enabling faster performance
- he servo motor is equipped with an absolute encoder, eliminating the need to search for the zero position upon startup
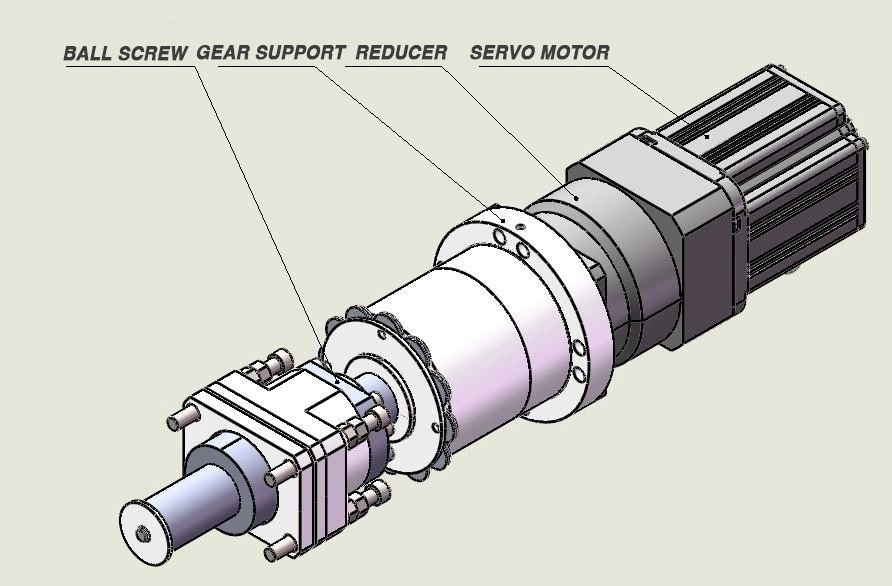
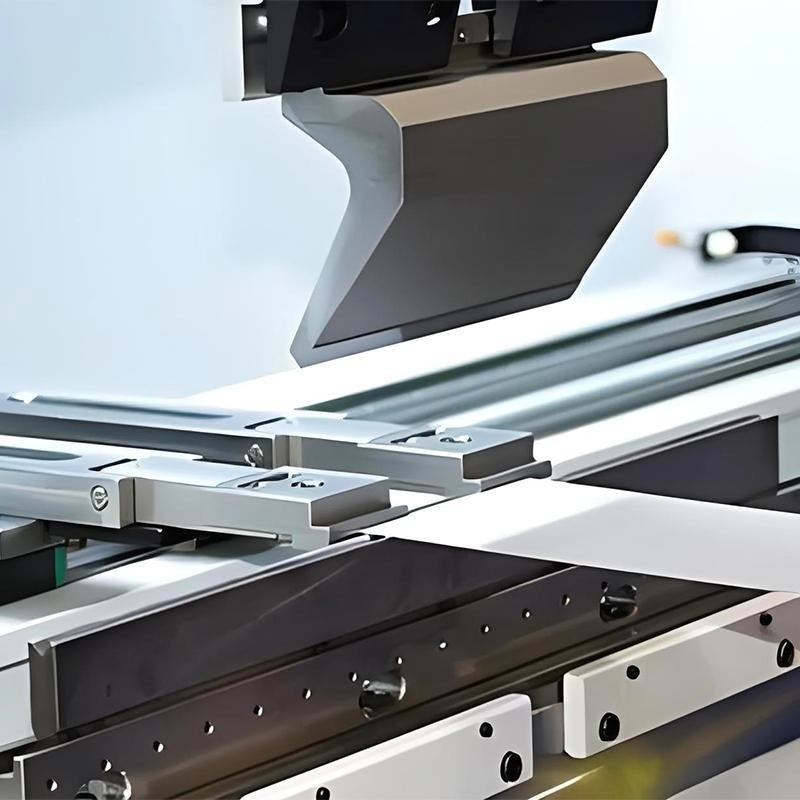
Pure Electric Press Brake Following Major Advantages
- The servo-driven system consumes power proportional to the load, significantly reducing energy usage. Minimal power is consumed when the slider is idle, unlike hydraulic machines that continuously draw power. The main transmission efficiency exceeds 95%, compared to less than 80% for hydraulic systems, with hydraulic efficiency further declining due to aging and wear.
- Eliminating hydraulic oil removes the need for oil changes, hydraulic component maintenance, and handling daily oil leaks. This reduces waste oil disposal and pollution. High slider speeds and production efficiency further contribute to eco-friendly operations.
- Adjustable bending speeds allow precise control for varying material thicknesses, types, and bending lengths, ensuring high accuracy (±0.5° angle error) compared to hydraulic machines (±1° error). The direct-drive system enhances transmission precision without requiring costly closed-loop systems
- Unlike hydraulic systems, which require regular oil changes and are prone to pump, valve, and seal failures, pure electric bending machines feature a simple transmission system with minimal maintenance needs, typically limited to periodic lubrication
Product Feature:
CAMT pure electric bending machines deliver twice the efficiency of hydraulic systems while consuming only half the energy
CAMT developed to meet market demands, featuring powerful functionality, rich built-in resources, and characteristics of safety, efficiency, energy savings, and environmental friendliness.
Advanced sheet metal bending and motion control algorithms, with the mainboard utilizing industrial-grade chips. The CNC system has passed EMC electromagnetic compatibility verification and high/low-temperature environmental adaptability testing.
All-Electric Servo Drive Press Brake:
Reliable Performance, High Precision under Fast Speed, Energy Saving
employs high-speed acceleration/deceleration and trajectory look-ahead algorithms, enabling pre-planned motion trajectories based on bending speed and vector characteristics before the bending process. This ensures optimal bending precision and smooth motion characteristics during high-speed operations, effectively integrating high speed with high accuracy.
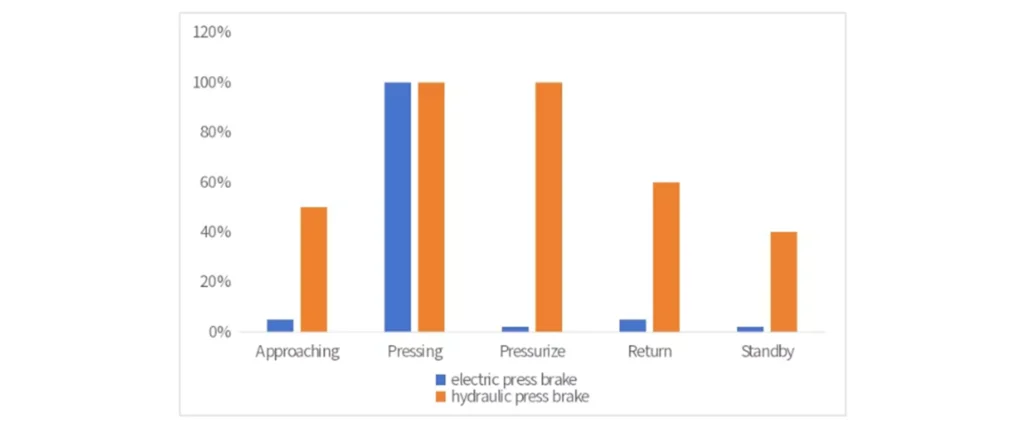
- Y-axis maximum rapid feed speed of 200 mm/s, maximum working feed speed of 30 mm/s.
- Repeat positioning accuracy of ±0.01 mm.
- Eliminates the impact of oil temperature variations on the consistency of bent workpieces.
Exceptionally Energy-Saving and Eco-Friendly
The all-electric servo press brake consumes electricity similarly to an inverter air conditioner compared to a conventional one, automatically adjusting power output based on operating conditions for exceptional energy savings.
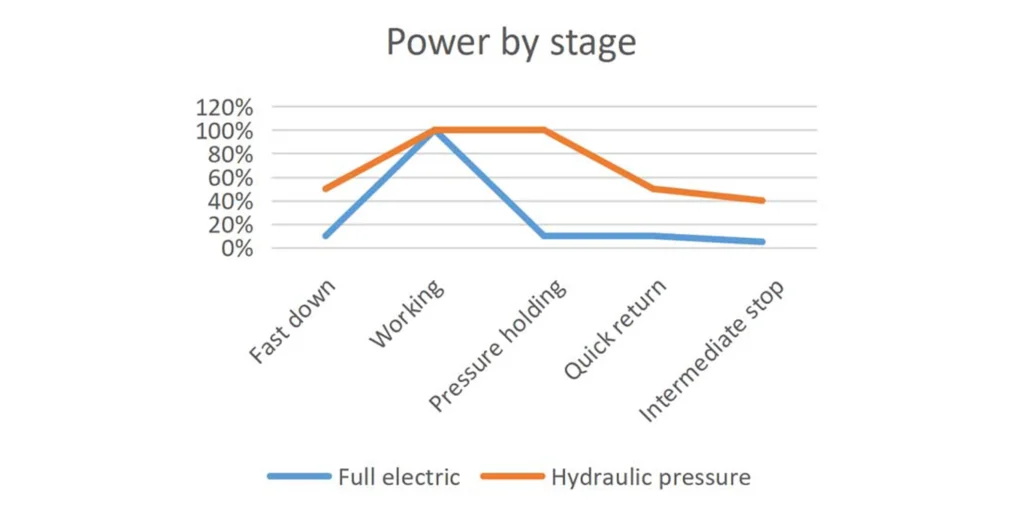
Eliminates the need for hydraulic oil and its replacement, preventing environmental pollution from waste oil.