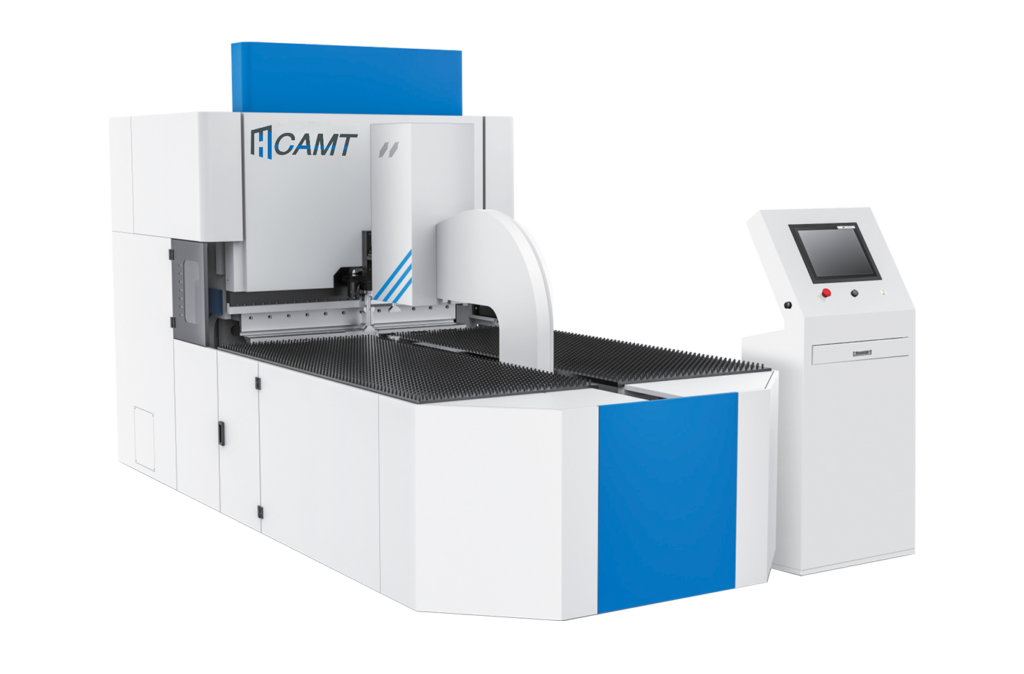
CAMT
Advanced Automatically Bending Cell
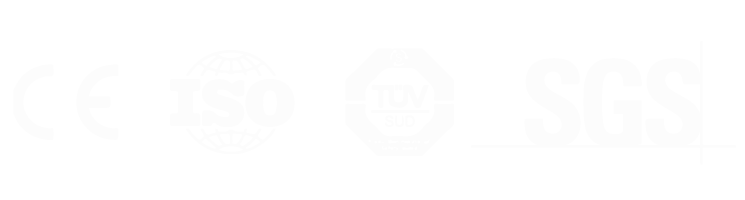
CAMT
Pressure Arm Type Flexible Bending Center
CAMT bending center is an advanced, automated sheet metal processing system designed for high-efficiency, precision bending of various metal components. Equipped with state-of-the-art CNC systems, servo-electric technology, and sophisticated algorithms, bending centers streamline the bending process by offering rapid setup, high-speed operation, and exceptional accuracy. These systems typically feature a modular design, integrating components such as servo motors, high-precision lead screws, and intelligent control systems to ensure flexibility, reliability, and minimal maintenance. The elimination of hydraulic systems makes bending centers energy-efficient and environmentally friendly, with features like low power consumption, no hydraulic oil usage, and reduced noise levels.
Automatically Panel Bending Center Solution
CAMT bending center’s ability to deliver high-speed, high-precision, and eco-friendly production makes it an essential tool for manufacturers seeking to enhance productivity, reduce operational costs, and meet stringent environmental and quality standards. Its versatility and automation capabilities position it as a cornerstone of modern sheet metal processing across diverse industrial sectors.
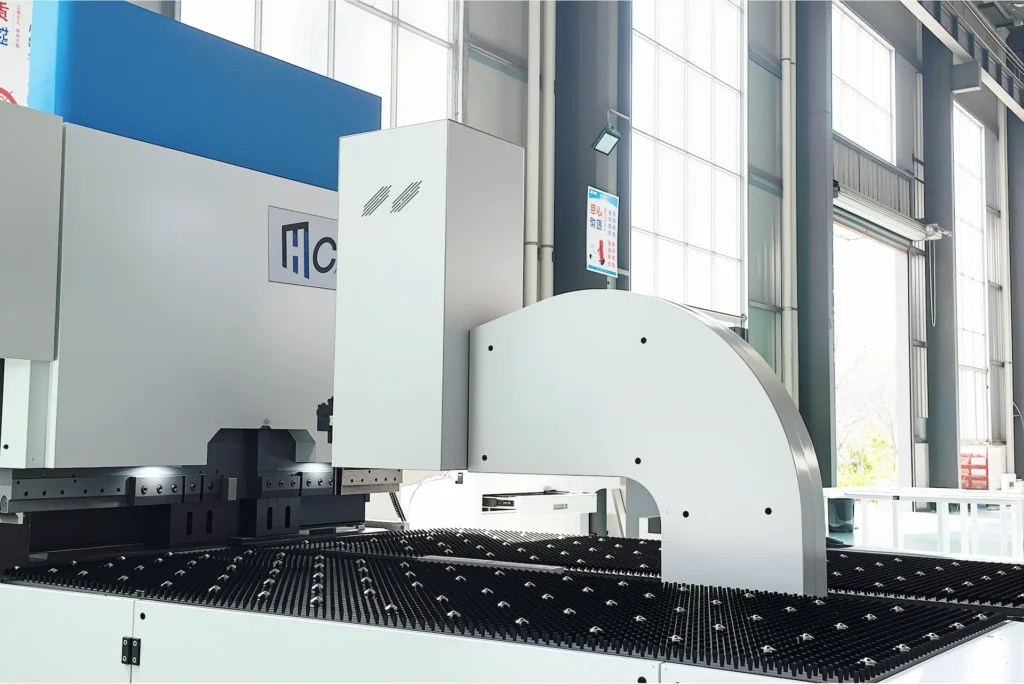
Key Features of Bending Centers
Capable of achieving rapid feed speeds (e.g., Y-axis up to 200 mm/s) and repeat positioning accuracy of ±0.01 mm, ensuring consistent, high-quality bends.
- Energy Efficiency
- High Speed and Precision
- Intelligent Control
- Versatility
Bending centers are widely used across industries requiring precise and efficient sheet metal fabrication, including:
Application
- Furniture Manufacturing: Producing metal frames and components for office and home furniture with complex geometries.
- Renewable Energy: Fabricating parts for solar panels, wind turbines, and energy storage systems.
- Electronics and Electrical Appliances: Producing enclosures, cabinets, and frames for devices like servers, air conditioners, and household appliances.
- Construction and Architecture: Creating structural elements, cladding panels, and decorative metalwork for buildings and infrastructure.
- Automotive Industry: Manufacturing components such as chassis parts, brackets, and panels with high precision and consistency.
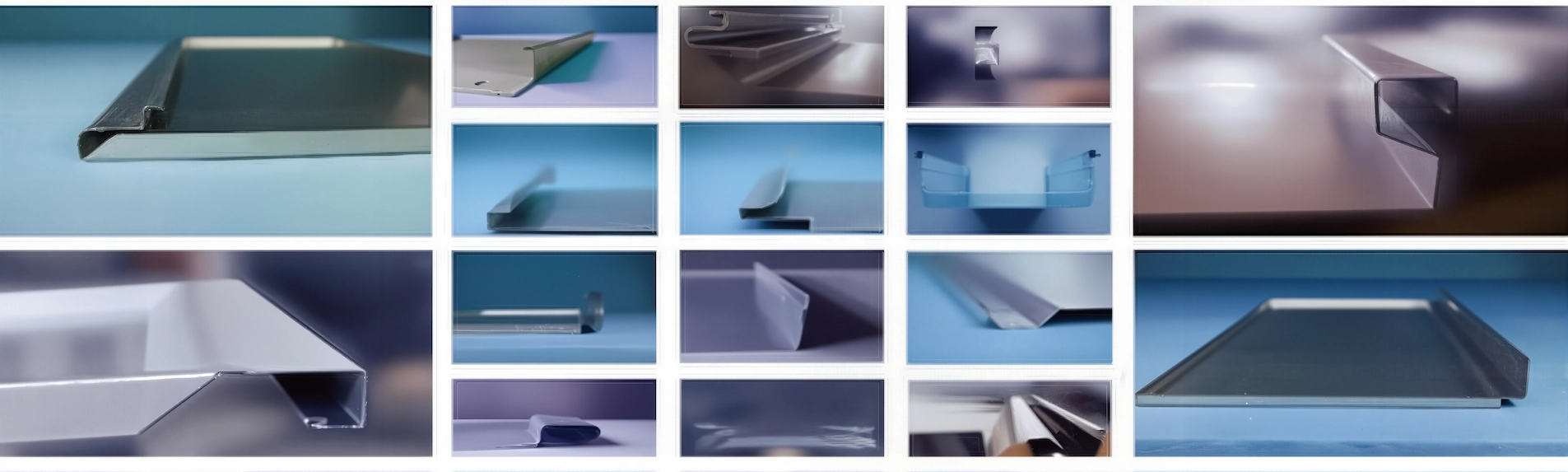
Complete intricate components in a single setup, enhancing efficiency and precision with the bending center's advanced automation and versatile capabilities.
AUXILIARY BLADES OPTION BENDIND TOOLS
Blank holders consist of segmented standard and bilateral horn blank holders.
The horn blank holders handle special shapes, like inward bends and work with fixed holders to enhance equipment functionality.
The automatic correction function can automatically adjust the C/C11 axis to compensate for sheet rotation errors.
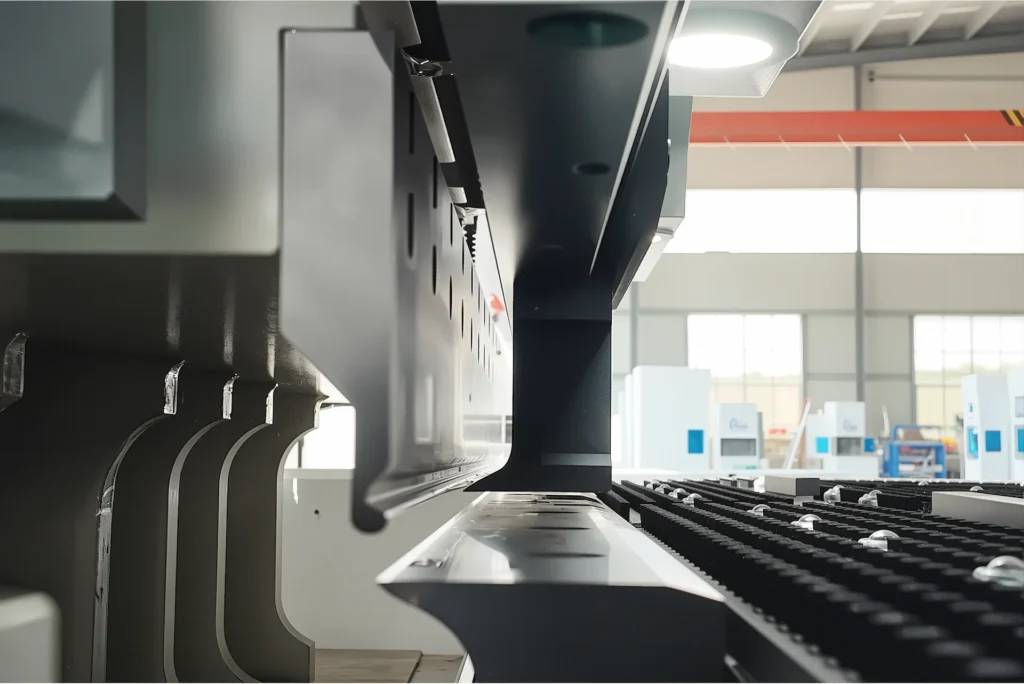
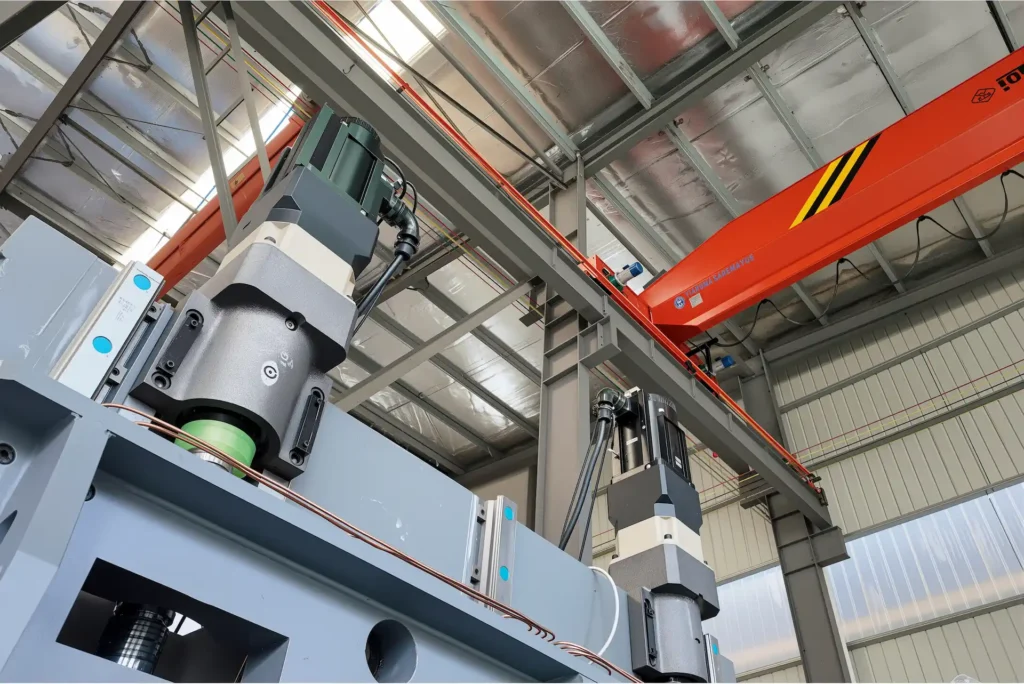
KINEMATIC CONTROL For Bending Center
VEICHI servo motor with a highprecision helical gear planetary reducer andheavy-duty grinding screw drives the bending toolalong a programmed path, ensuring a stable, efficient structure and easy maintenance.
SERVO MANIPULATOR
Full servo closed-loop control system, to realize the workpiece rotation at any angle, feeding and rotation linkage, reduce the workpiece rotation, feeding and positioning time, improve production efficiency.
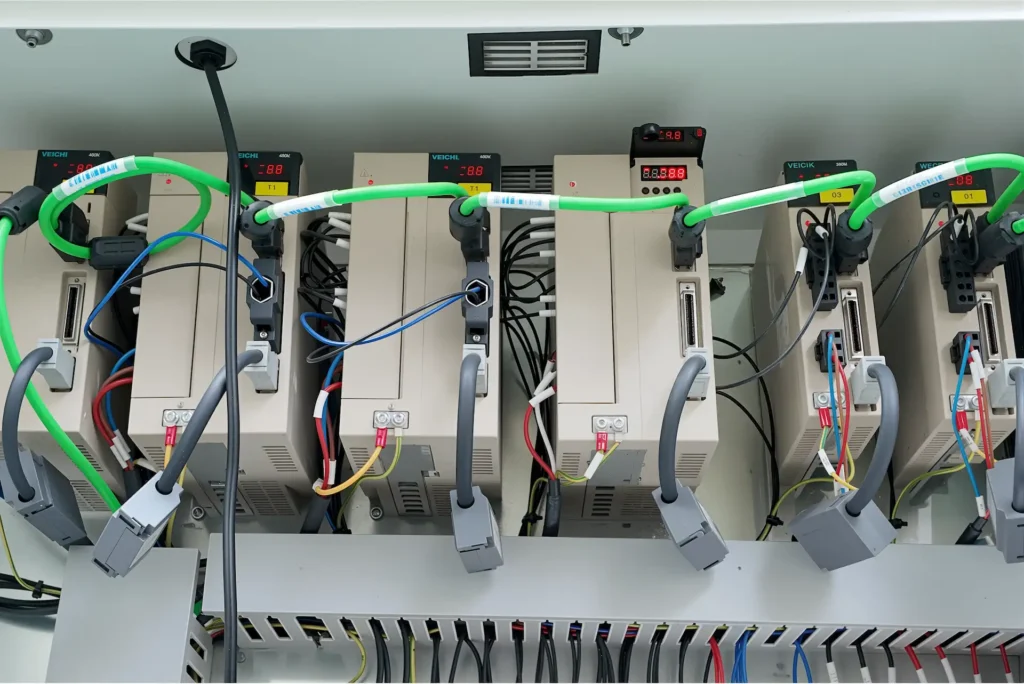
Production Processing of Bending Center
- High standard castings: The core framework of the equipment adopts high standard QT500-7 and HT250 castings, and the cast parts are measured bytesting instruments after being fired. The framework undergoes precise finite element stress analysis and adopts a stable triangular interconnection design, greatly ensuring stability under high tonnage impact forces.
- High standard welding: Carbon dioxide shielded welding is used throughout the entire welding process, and full weldingl process is used at the welding site to ensure that the welded workpiece is firm and aesthetically pleasing.
- Stress relieftreatment: The support table for castings and welding adopts a high-precision temperature controlledl furnace, and undergoes multiple heat treatment processes such as tempering and annealing according to the temperature curve corresponding to the material. After a long period of full frequency vibration aging treatment, the internal stress of the workpiece is released, and it does not deform after long-term use.
- Precision machining: Different fixtures are designed for different workpieces, and high-precision multi axis machining centers are used to perform precision machining on the workpieces, ensuring consistency in accuracy before and afterl clamping.
- Strict testing: Using a high-precision micrometer U-meter, combined with a marble platform and a marble square withl a longer service life, precise measurements are taken for each workpiece, and the processing quality of each workpiece is strictly controlled, layer by layer, to ensure that the assembly accuracy ofthe entire machine meets the standards ofl high-precision machine tools.
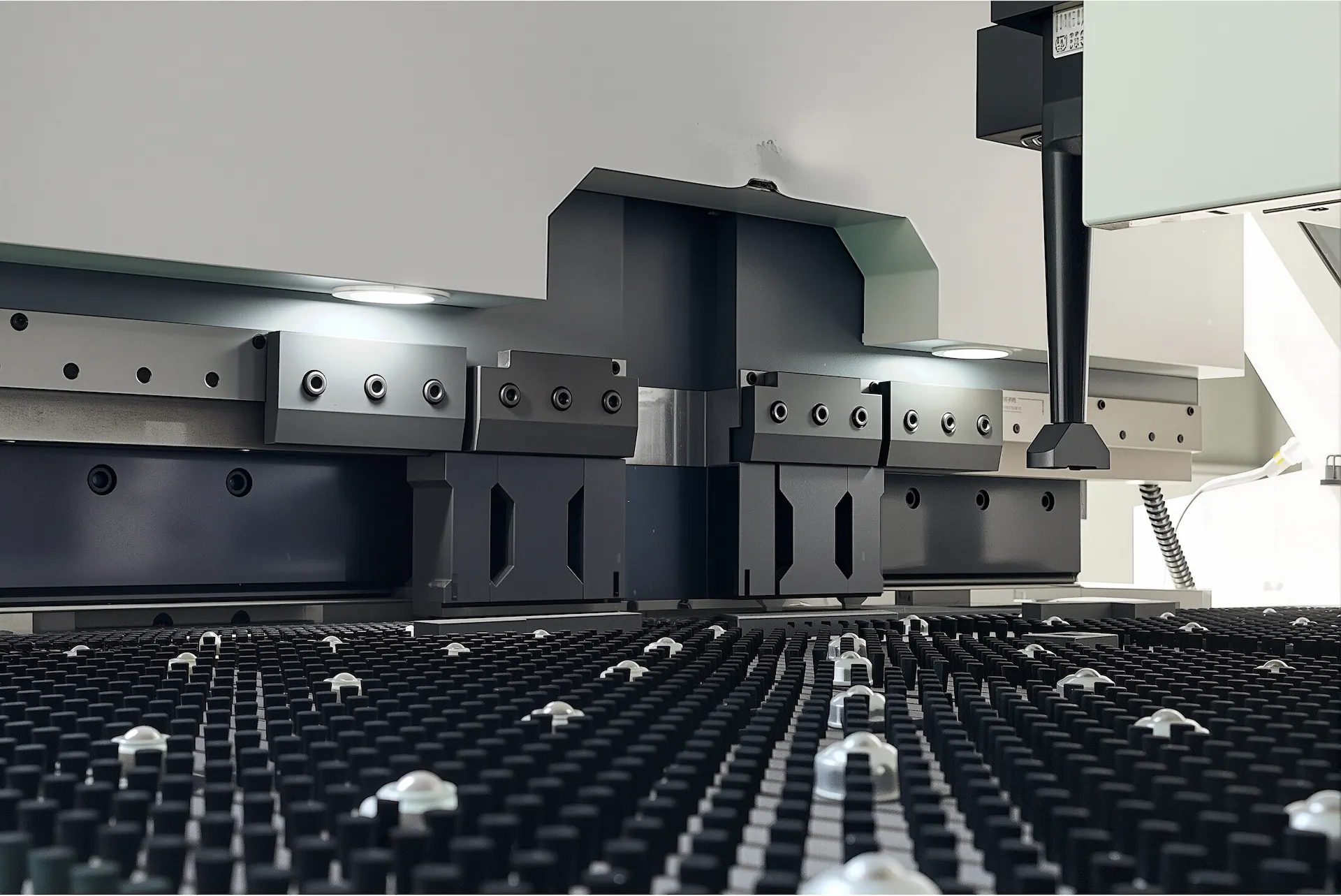
Automatic Bending Center Solution Advantages
- Fully automatic folding, high efficiency, energy-saving, and environmentally friendly.
- Bus control, which can be directly connected to the Internet of Things for remote control and grid monitoring.
- Dual servo rotation with automatic downward pressure structure, quick downward pressure, adjustable pressure, and high positioning accuracy for rotation.
- Easily achieve sheet metal bending requirements for circular arcs, reverse folding and flattening, return molding, closed molding, and other complex shapes.
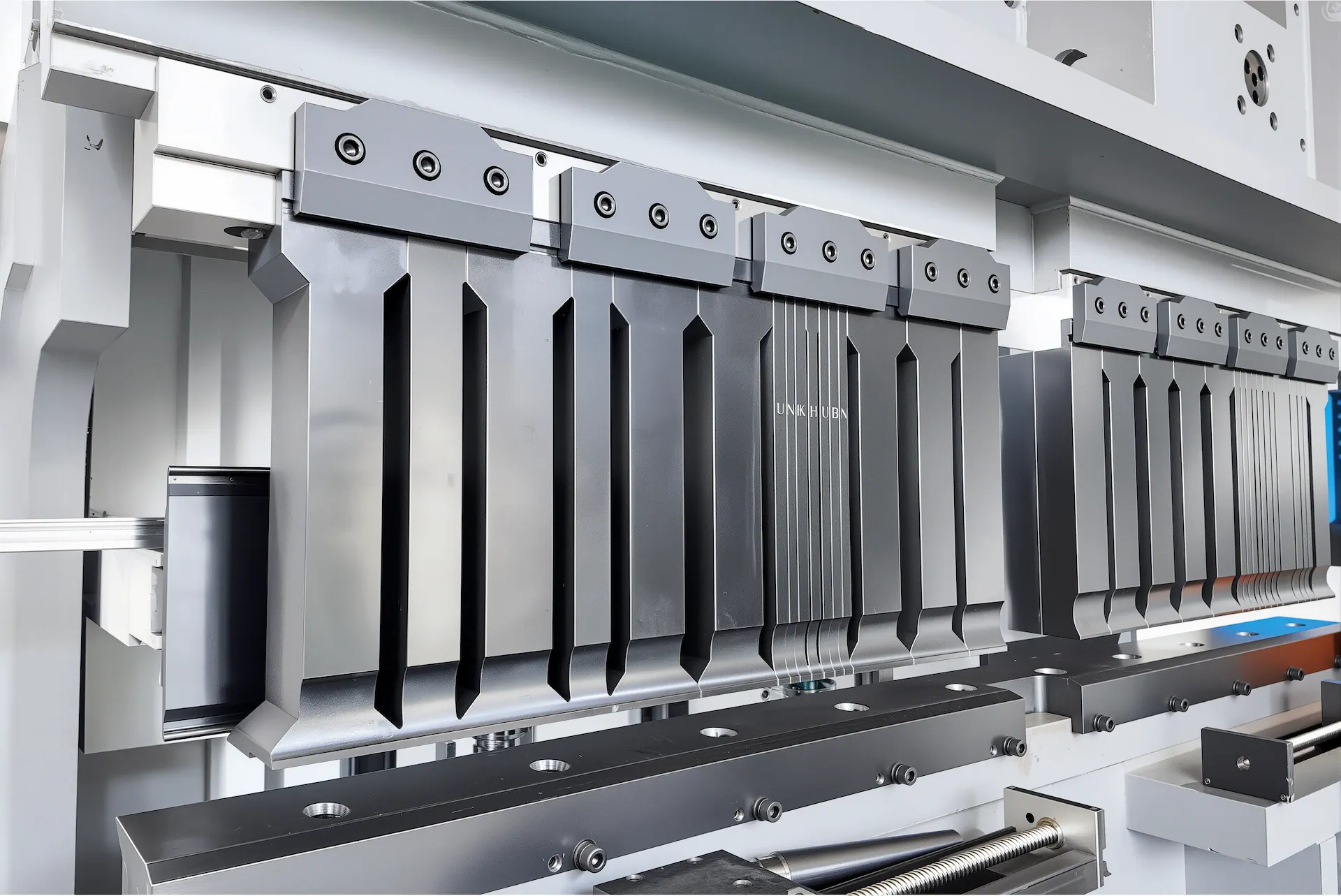