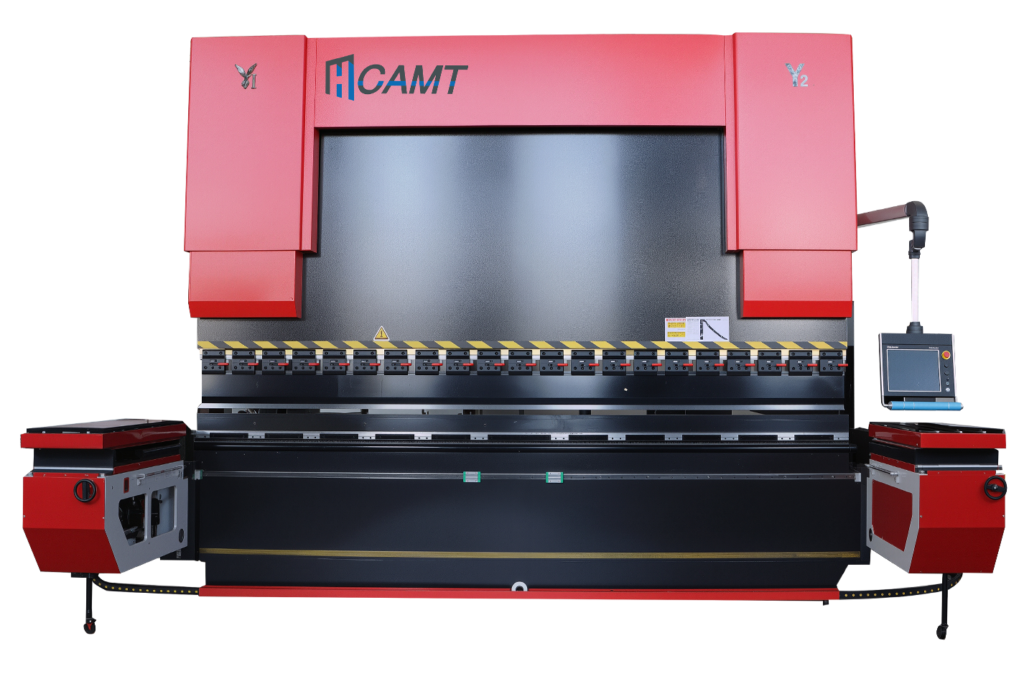
CAMT
Heavy Duty Super Press Brake
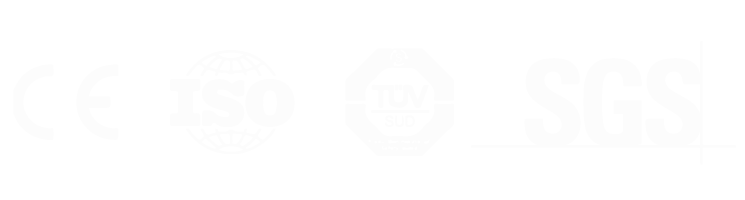
CAMT
Heavy Duty Super Press Brake
Long&Thicker Sheet Metal Processing Best Solution
CAMT®️heavy duty super press brakea high-performance hydraulic or CNC-controlled bending equipment designed for processing large and heavy metal plates, widely used in heavy industry.Indicates a maximum bending force and a longer worktable length . Typically equipped with an electro-hydraulic servo system or full CNC system, it features high-precision sensors, servo valves, and advanced control software to achieve high-accuracy bending of metal plates.Similar heavy-duty CNC bending machines, have a robust welded steel frame (usually made of Q235 A1 high-strength steel) capable of withstanding high loads and continuous operation.
It is suitable for processing thick carbon steel, stainless steel, aluminum alloys, and other materials, with a maximum bending thickness typically ranging from 10-12 mm (for carbon steel, depending on material and mold configuration).
Popular Configuration
- 21.6-inch color high-definition touch screen with friendly human-machine interface
- CHTR Rear BGA 600MM with 300MM/S
- 4 V Double CNC die series &835mm punches
- High Precision & Multi Point Mechanical Crowning
- Imported Italy GIVI Maganetic Misure
- FULL Close-loop High Performance Hydrauic System
- All-In-One Effective Servo Motor
- Graphite Self-lubricating Copper Plate
- Safety France Schneider Electric System Components
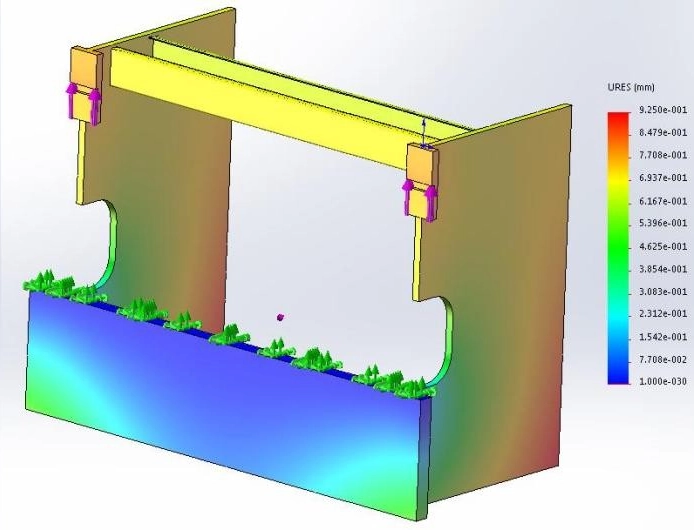
FEA & Stress Analysis of Press Brake
Stress Analysis & Finite Element Analysis
DELEM CNC Control System
DELEM DA66T Touch 2D Graphical Control
- 17" high resolution colour TFT
- 2D graphical touch screen programming mode
- 3D visualisation in simulation and production
- Full Windows application suite
- Delem Modusys compatibility (module scalability and adaptivity)
- USB, peripheral interfacing
- Profile-T2D offline software
- Sensor bending & correction interface
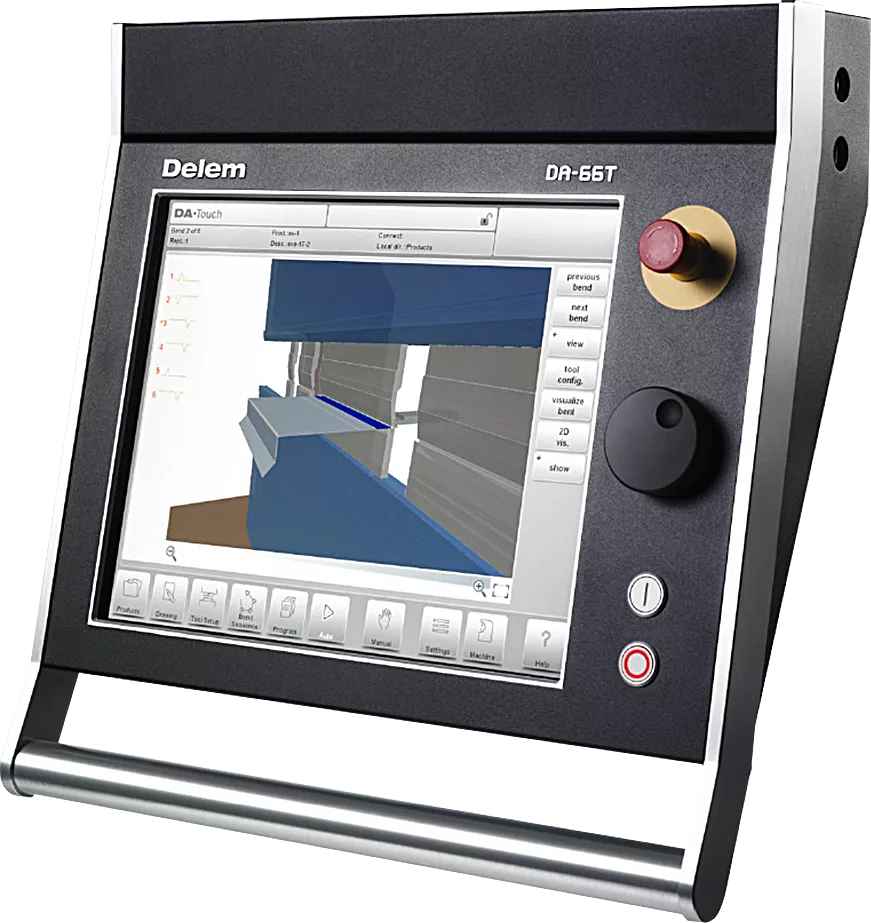
Intergral Advanced CNC Control System
More Than 10 Years R&D CNC Control
- 21..6-inch color high-definition touch screen with friendly human-machine interface
- "One-page" programming navigation, one page can display all data, and it isfaster to modify the curve information
- The system supports 4-axis control, meeting the highest control conditions of 4+1+2 axis bending machine
- The Linux operating platform is stable and reliable, with fast startup speeddand can be directly powered off and shut down
- The bending data is automatically calculated, the bending speed of each step is programmable, the slow down and mid-stop can be controlled, and thehome page has convenient functions such as fast mold alignment, so novicescan quickly get started
- Rich interfaces, can be easily and conveniently connected to the automateddproduction line as a bending unit
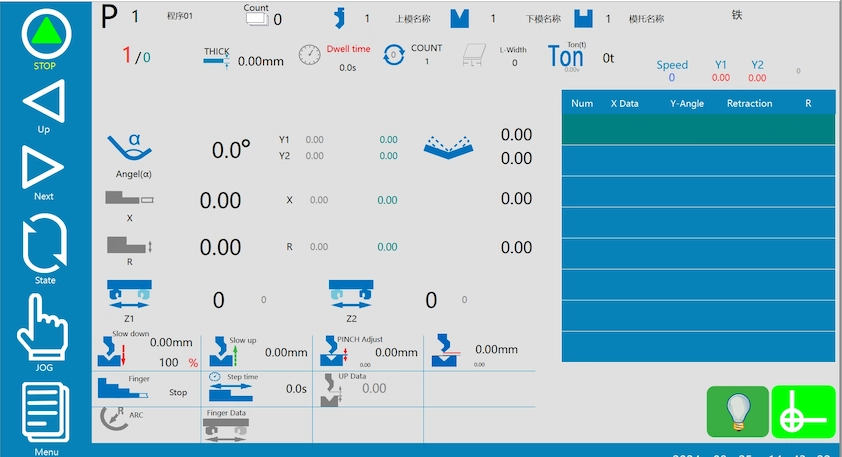
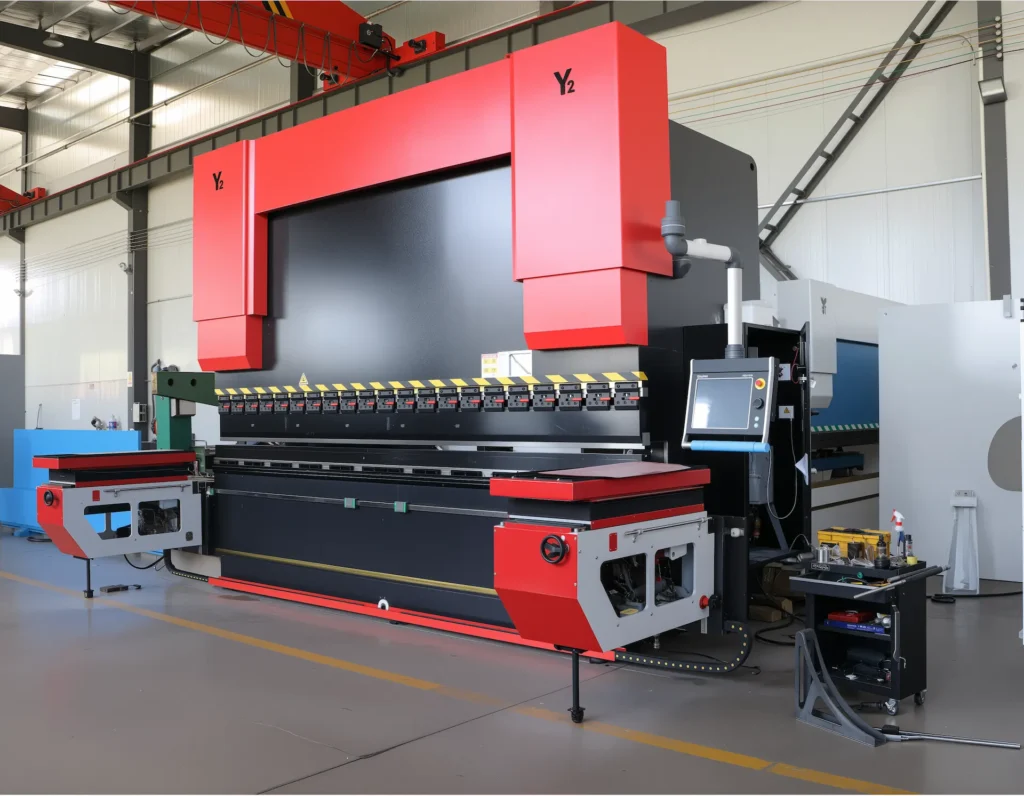
Heavy Duty Structure Bending Machine
High Strength & Stability Large Press Brake
designed for processing large workpieces, accommodating ultra-long , wide, or heavy plates, and is widely used in manufacturing for ships, bridges, steel structures, wind turbine towers, and pressure vessels. It supports complex shape processing through CNC programming, enabling multi-angle and multi-stage bending to meet intricate geometric requirements. High-precision production is ensured by synchronous control and backgauge systems, maintaining consistent bending angles and dimensions for industrial components with stringent accuracy demands. The machine facilitates batch production with multi-program storage making it suitable for mass production or single-piece customization. Its versatility spans multiple industries, including steel structures, rail transportation, aerospace, and energy equipment, processing components such as lamp poles, carriage panels, and building curtain walls.
Optional Safety Arrangement - Light Curtain
- Electro-hydraulic servo system and grating ruler feedback ensure slider synchronization accuracy within ±0.01 mm
- High backgauge positioning accuracy (±0.05 mm), ideal for precision parts production
- Automatically calculates bending force and stroke, reducing setup time and supporting quick mold changes and programming
- Supports various mold configurations to meet different thickness and material processing needs
- Optional features like automatic mold changing, variable V-groove molds, and automated loading/unloading systems enhance production automation
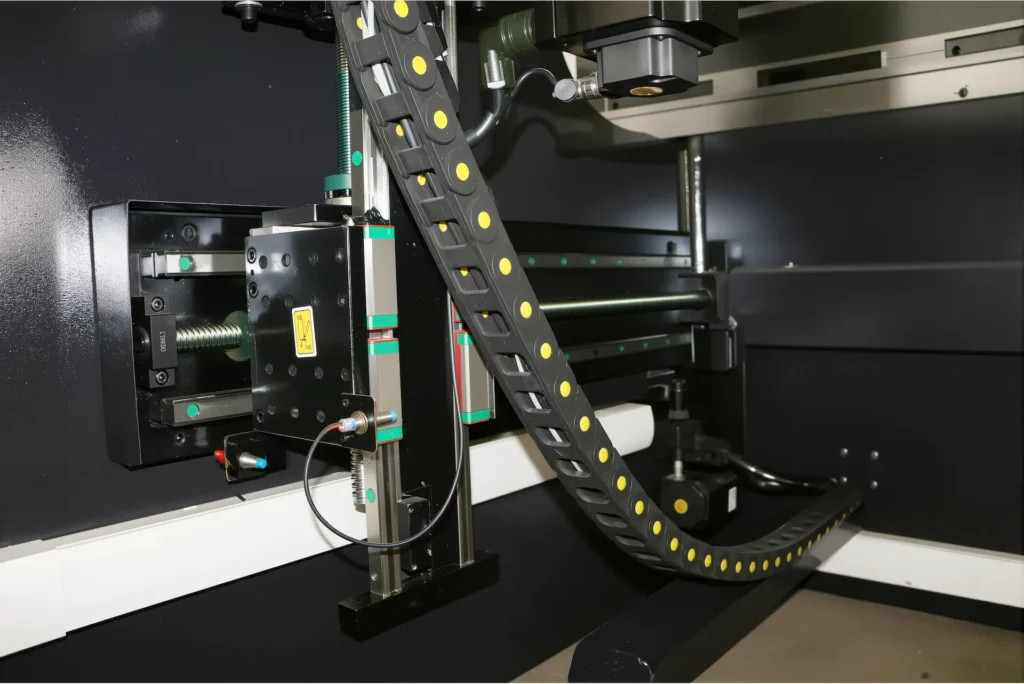
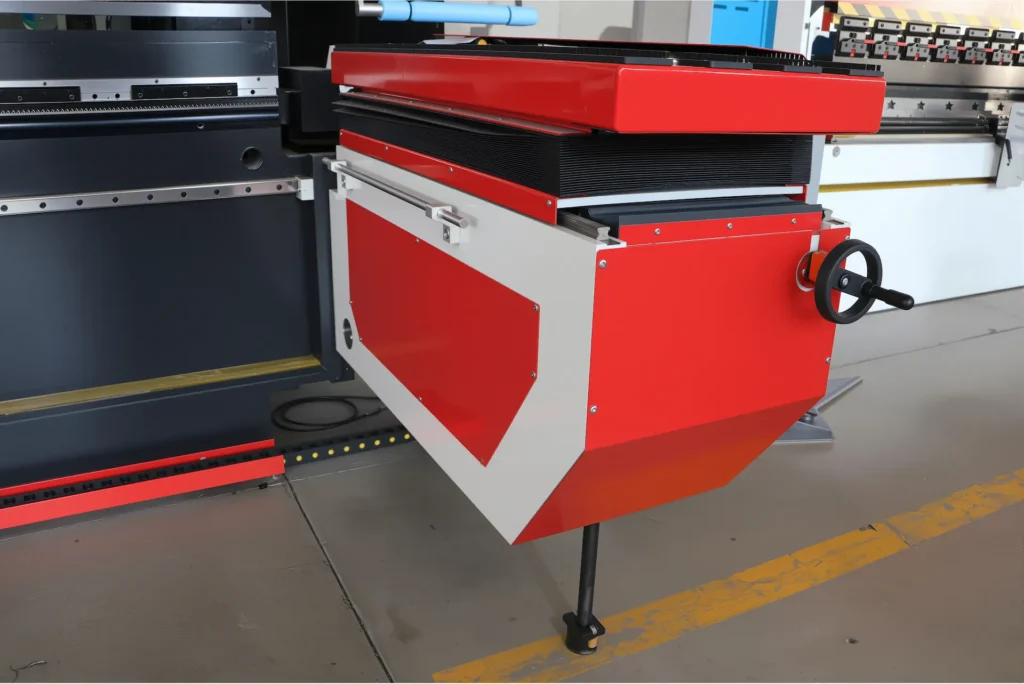
Bending Follower
Role and Advantages of the Follow-Up Device in Bending Machines
Press brake bending Follower(also known as a follow-up support or material support) primarily assists in processing large or thin workpieces by providing a synchronized support platform that moves with the slider to hold the plate, preventing sagging or deformation due to its weight or bending force. The device automatically adjusts its height and angle based on the workpiece size and bending angle, ensuring stability during processing. Its advantages include improved processing accuracy (avoiding angle deviations), enhanced workpiece quality (reducing surface scratches or deformation), increased safety (reducing operator workload), and wide applicability (suitable for ultra-long or ultra-thin plates), making it highly effective in large-scale plate bending for industries like shipbuilding and steel structures.
Industrial Air Conditioning in Bending Machine Operations
- Provides comfortable temperature and air quality for operators, reducing thermal stress and boosting work efficiency
- Reduces equipment failure rates and lowers maintenance costs
- Modern industrial air conditioners use inverter technology and heat recovery to minimize energy consumption
- Customizable to suit various workshop environments and meet the needs of different bending machines
- Stable conditions minimize risks of equipment overheating or operational errors
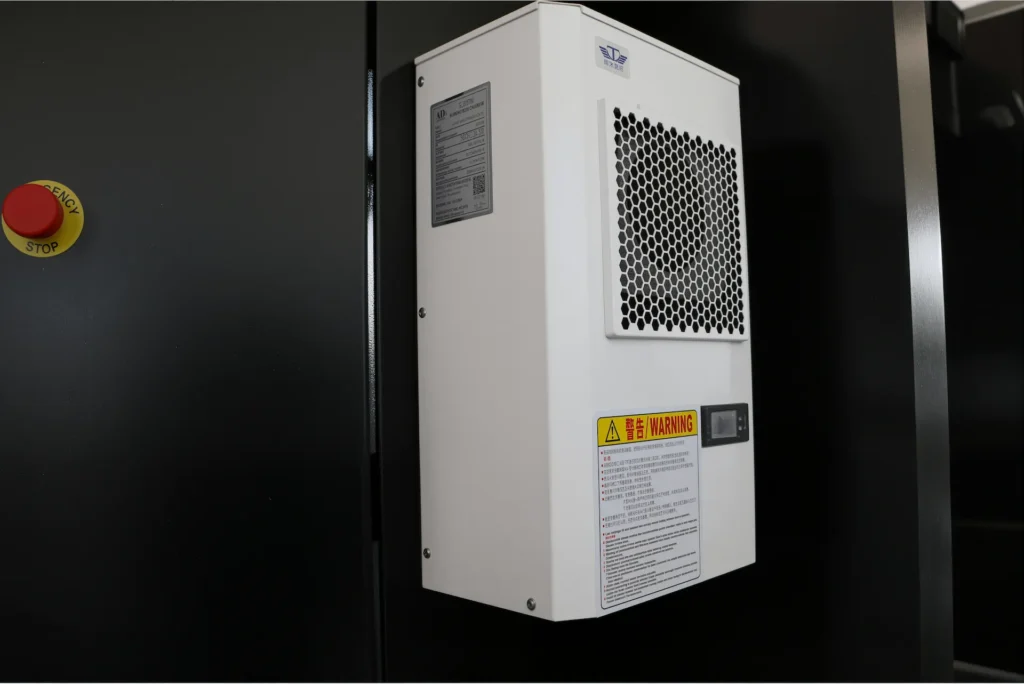
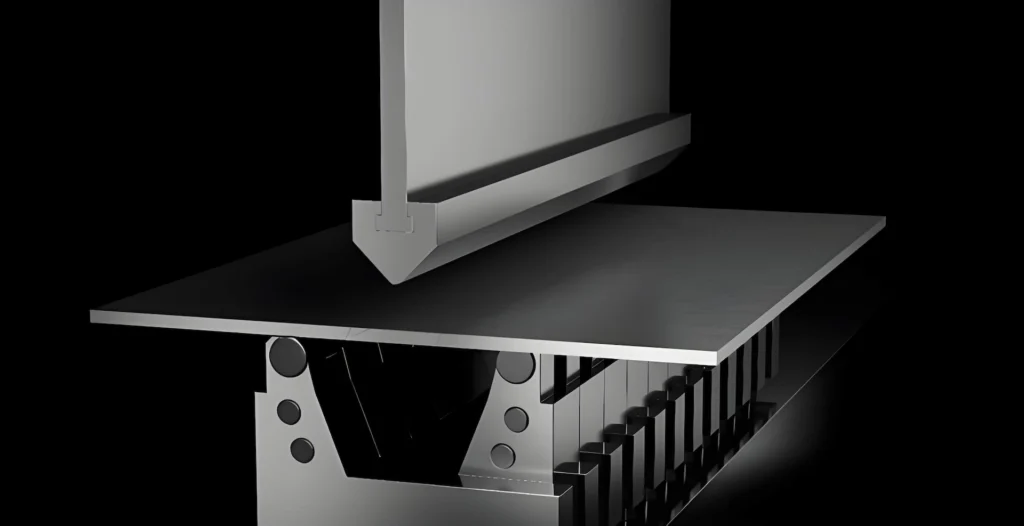
Adjustable Big V Die
Advantage:
- Used for various complex metal processing tasks, overcoming challenges in traditional bending applications
- Bending accuracy can reach 30 degrees, depending on the synchronization capability of the machine
- Compared to traditional models, reduces bending pressure by 10%
- Overcomes issues of material deformation, reducing model replacement time by 30% or more
- Compared to traditional models, consume less energy in operation, making them more user-friendly
- Can be conveniently transported and added to workpieces (models), supporting customer-added integrated operations
CAMT Itergral Hydraulic System
Advanced Hybrid Servo ECO Technology
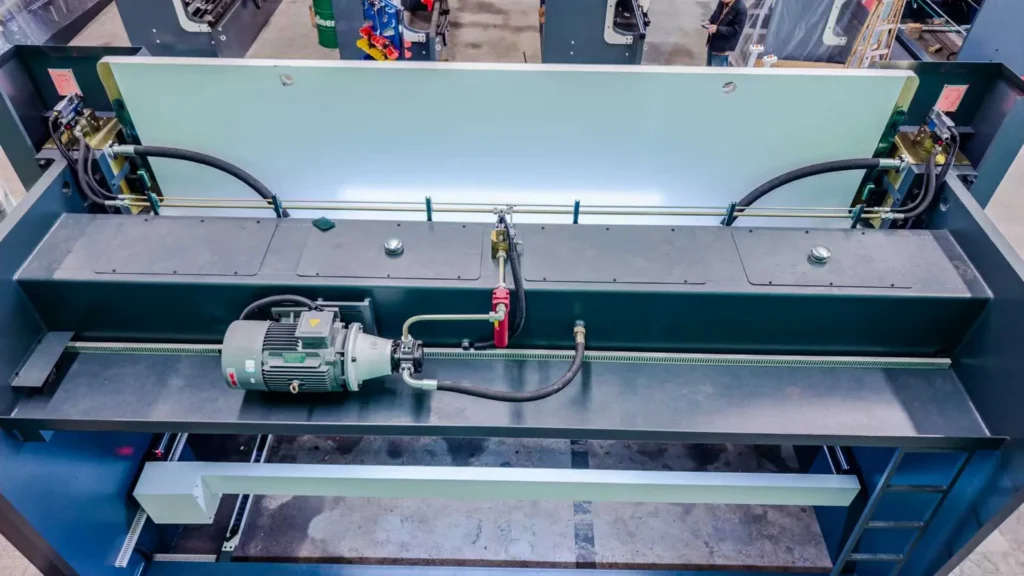
Advantage:
- Ensures machine stability and rigidity with strict inspections and finite element analysis.
- Delivers real-time feedback and micron-level precision.
- Boosts efficiency with 20% faster response than hydraulic systems.
- Eco-friendly design with regenerative power recovery.
- Advanced technology for superior performance.
- Automatic angle correction and collision prevention.
- Backed by professional engineers for lifelong assurance.
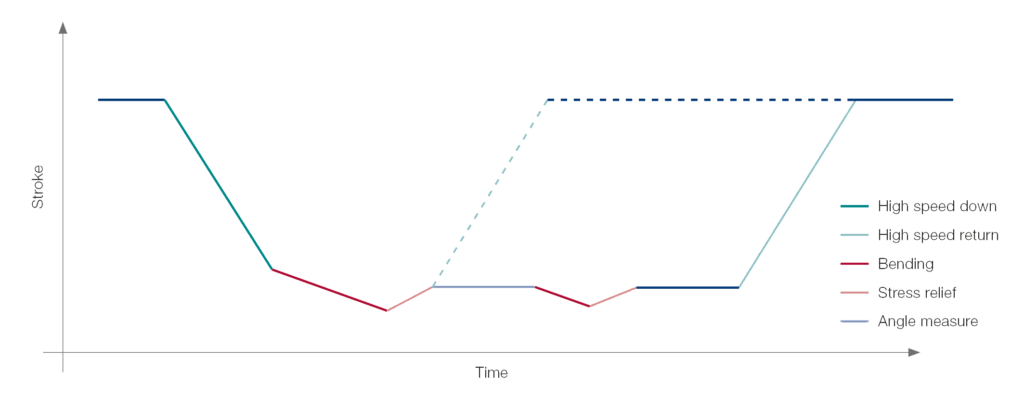