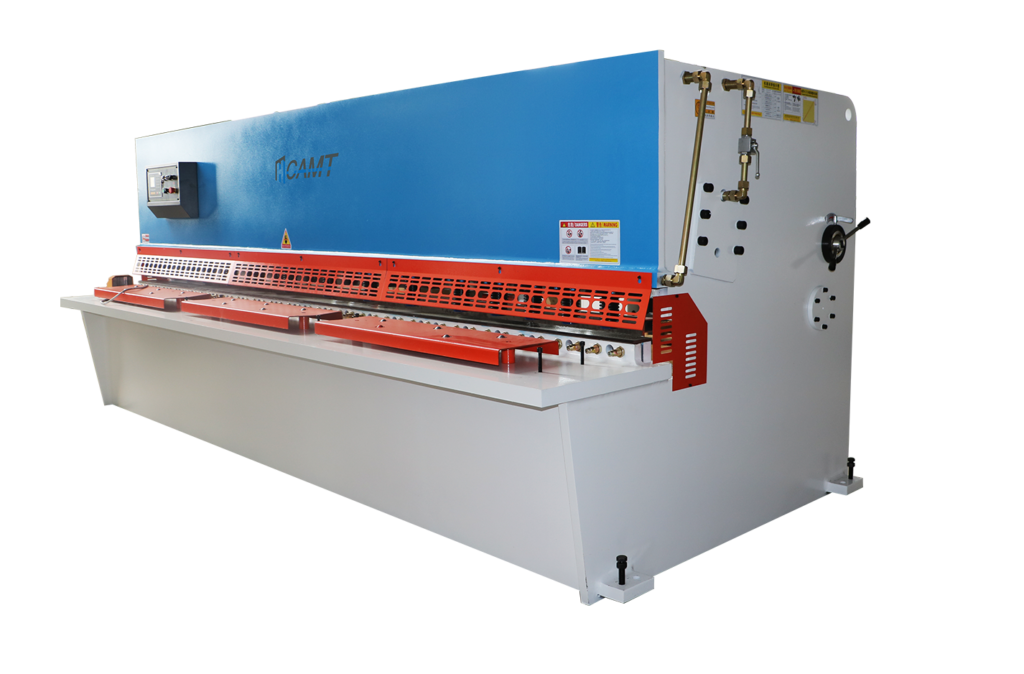
CAMT
QC12Y Swing Beam Type Hydraulic Shears
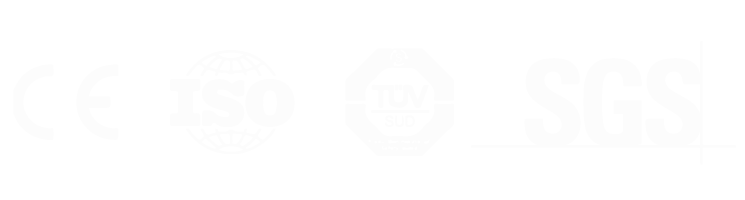
QC12Y Swing Beam Type Hydraulic Shears
Precision and superior quality handles various materials and thicknesses.
High Performance Cutting, Effecient Speed
CAMT hydraulic shearing machine is a kind of machine that uses a moving upper blade and a fixed lower blade, and uses a reasonable blade gap to apply shearing force to metal plates of various thicknesses, so that the plates can be separated according to the required size.
When the oil cylinder at the left end of the machine enters the oil, the piston descends, and at the same time the oil enters the piston at the right end cylinder to descend, thereby ensuring the parallel movement of the tool post. When the amount of oil in the tandem oil circuit increases or decreases, the shear angle of the tool post changes accordingly. When cutting two copper plates, the four corners of the shear are reduced, which can not only ensure that the plate is not twisted, but also shorten the stroke of the tool post, which can also increase the stroke frequency per minute. This kind of structure often uses a nitrogen accumulator to push-one or two return cylinders to shorten the inter-travel time, thereby increasing the productivity of the machine.
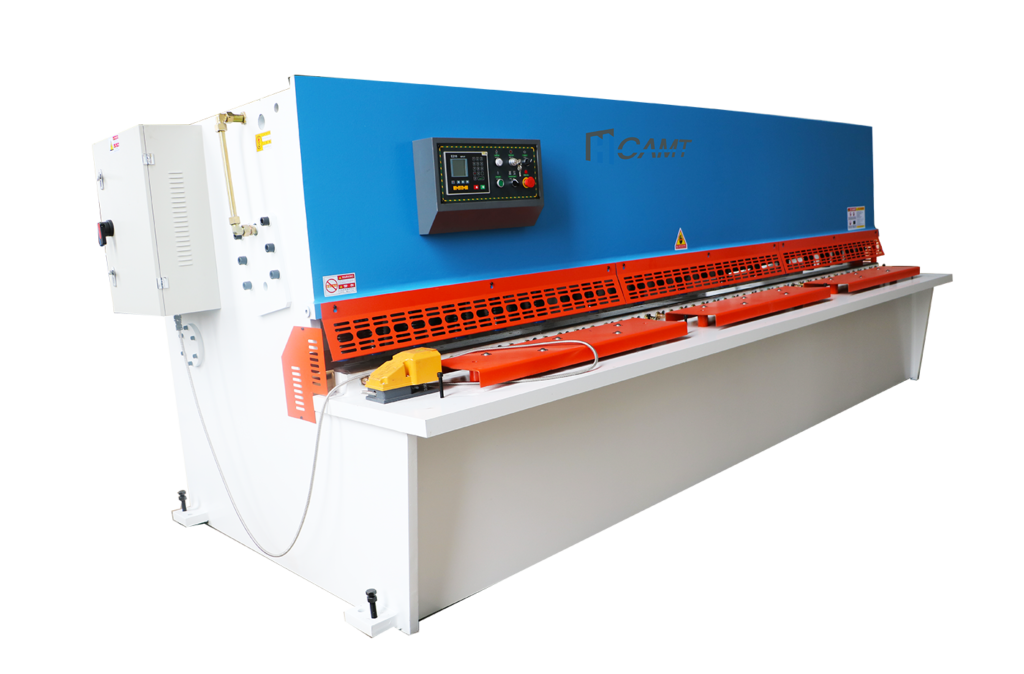
High Precision
Effecient Speed
Durable Quality
Versatile Application
Standard Equipment
- Estun E21S Digtal Display Simple Control
- Taiwan UOSHEN hydraulic system
- Ball screw BGA 600 mm
- High Precision BGA Control
- Automatic precise adjustment of the rear stop position
- Tool holder guide rail structure supported by three-point rolling path
- The shear angle adopts an adjustable device
- USA SUNNY/FIRST Gear Oil ump
- Powerful Mian Motor & Drive
- France SCHENEIDER Electric System
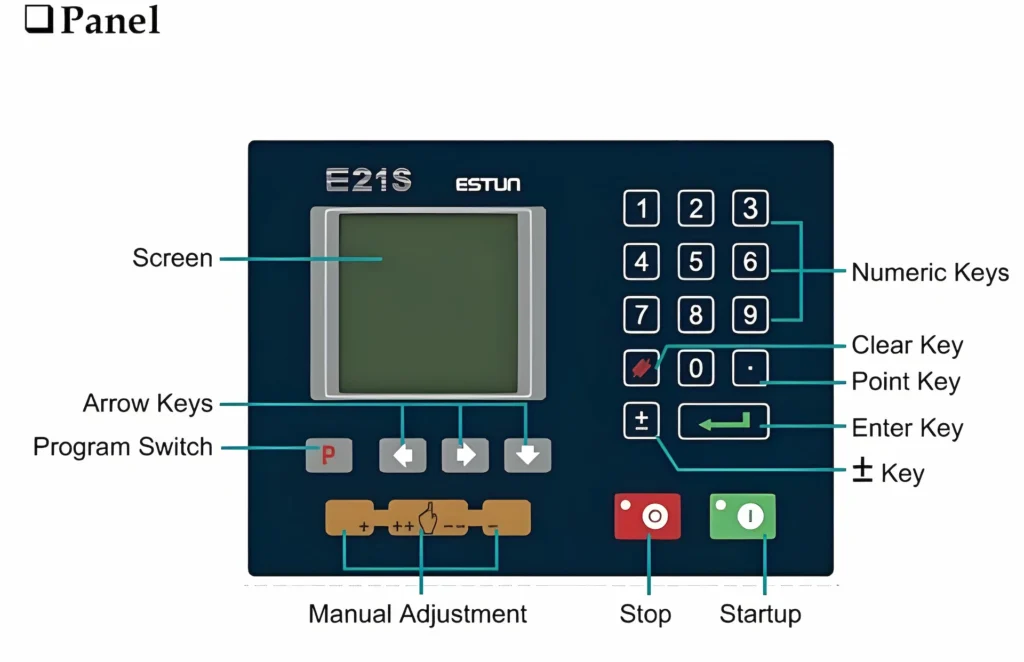
ESTUN E21S Simple Digital Control
- Back gauge can be controlled
- Cut-angle can be controlled
- Cut-gap can be controlled
- Stroke time can be controlled
- Intelligent positioning control
- Unilateral and bidirectional positioning
- Retract functions
- Automatic reference searching
- One-key parameter backup and restor
- Fast position indexing
- 40 programs storage space, each program has 25 steps
- Power-off protection
DAC-360T featuring:
- 7" widescreen TFT Colour LCD display
- Back / front gauge control
- Panel based housing
- Retract function
- Cutting angle and gap control
- Stroke length limitation
- Manual movement of all axes
- Force control
- Return to Sender function
- Program memory for 100 programs
- Sheet support system
- Sheet thickness measurement system
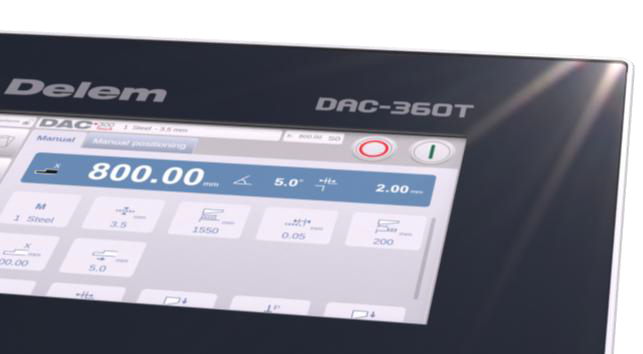
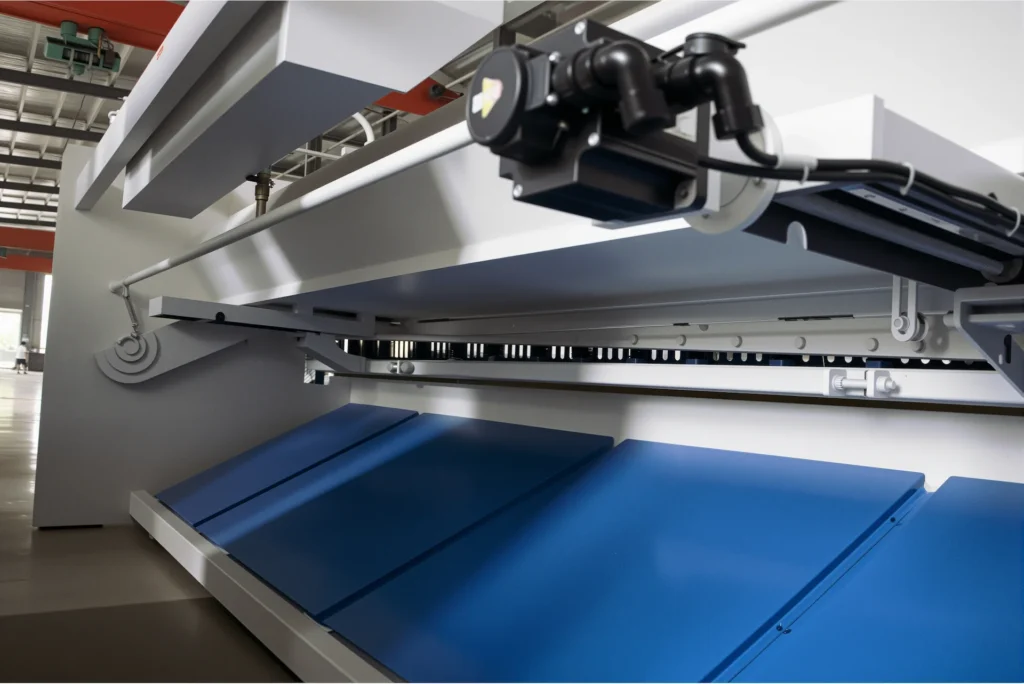
BGA Accurate & Fast BGA System
CAMT BGA moves with the upper knife holder in an up-and-down swinging motion. The adjustment of the rear gauge is driven by servo motor, which transmits power through gear reduction and a lead screw. When pressing the “+” or “-” adjustment buttons, the gauge plate can be adjusted forward or backward (with digital display of the position dimension). If the motorized adjustment cannot achieve the desired value, the manual adjustment wheel can be rotated for fine-tuning to ensure the required setting. Thus, the rear gauge adjustment is convenient and reliable. When the length of the sheet to be cut exceeds the maximum gauging distance of the rear gauge, the gauge plate can be moved to the rearmost position and lifted to allow cutting of sheets of any length.
WHY CAMT SHEARS
- Fast and high accuracy
- Reliable movement
- Adjustment at any point
- Resistance to crash
- Maintenance free
- Better and fast cutting
- Easy and secure usage
- High precision and repeatability
Pneumatic Sheet Support System for Precision Shearing Machine
CAMT pneumatic material support system of the shear machine utilizes air cylinders driven by compressed air to automatically raise and lower the support frame. During shearing, it stabilizes the material to prevent sagging and deformation, ensuring cutting precision. Compared to mechanical or manual supports, it offers advantages such as easy adjustment, rapid response, stable operation, simple maintenance, and energy efficiency. It is particularly suitable for automated cutting of large, heavy, or high-precision sheet metal, significantly improving production efficiency and processing quality.
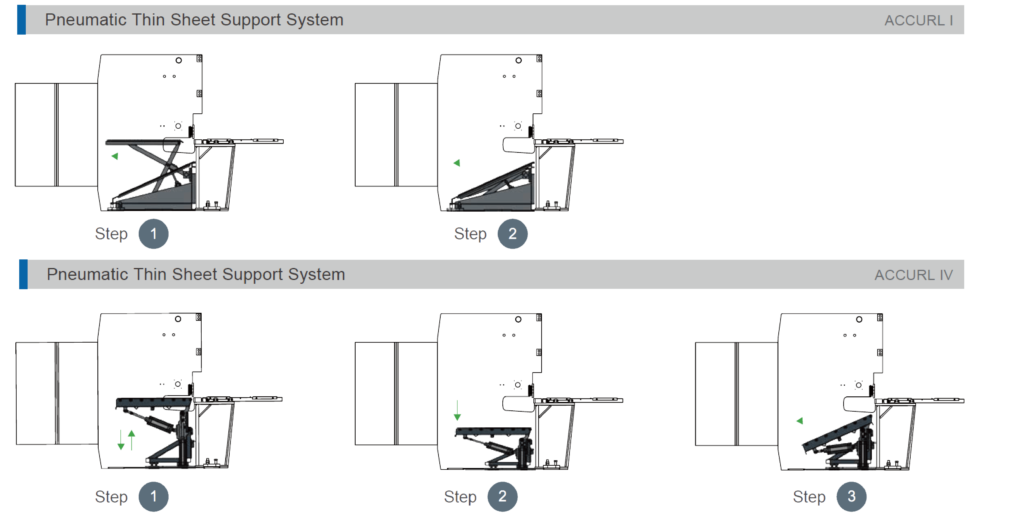
Shear Distortion Prevention: Principle and Function
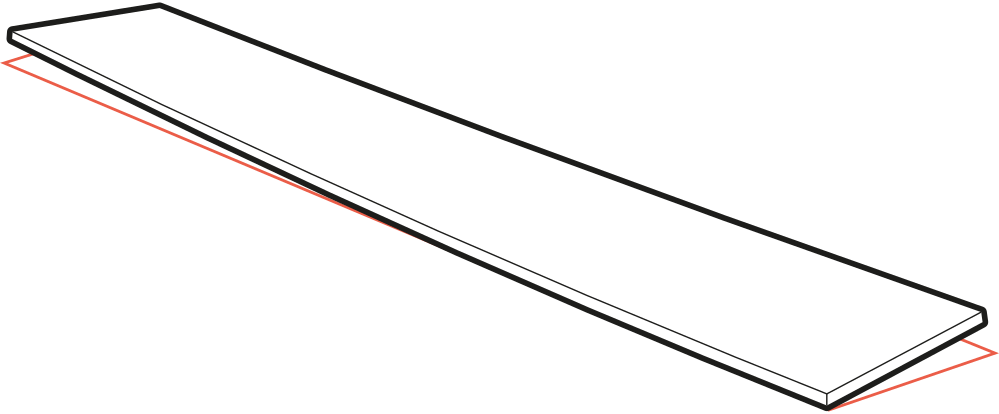
The Anti-Twist System of a hydraulic guillotine shear prevents distortion of sheet material during cutting by employing stable clamping and guiding mechanisms. Its working principle involves securely fixing the sheet through clamping devices or guiding structures to restrict horizontal movement. Simultaneously, the system ensures even distribution of cutting forces, minimizing localized stress concentration to prevent deformation in narrow or thin strips. Additionally, the Anti-Twist device collaborates with the hydraulic system to dynamically adjust clamping force based on material thickness and type, maintaining sheet flatness under various cutting conditions.
The Anti-Twist System significantly enhances the processing precision and efficiency of hydraulic guillotine shears. Its key functions include preventing material distortion during narrow or thin sheet cutting, ensuring smooth cutting edges; reducing sheet sliding and deformation to protect delicate surfaces (such as polished stainless steel or pre-painted plates) from scratches; and improving production efficiency by minimizing rework through a stable cutting process. Furthermore, the system expands the machine’s application range, enabling efficient handling of materials requiring high precision or superior surface quality, thus meeting diverse industrial processing needs.
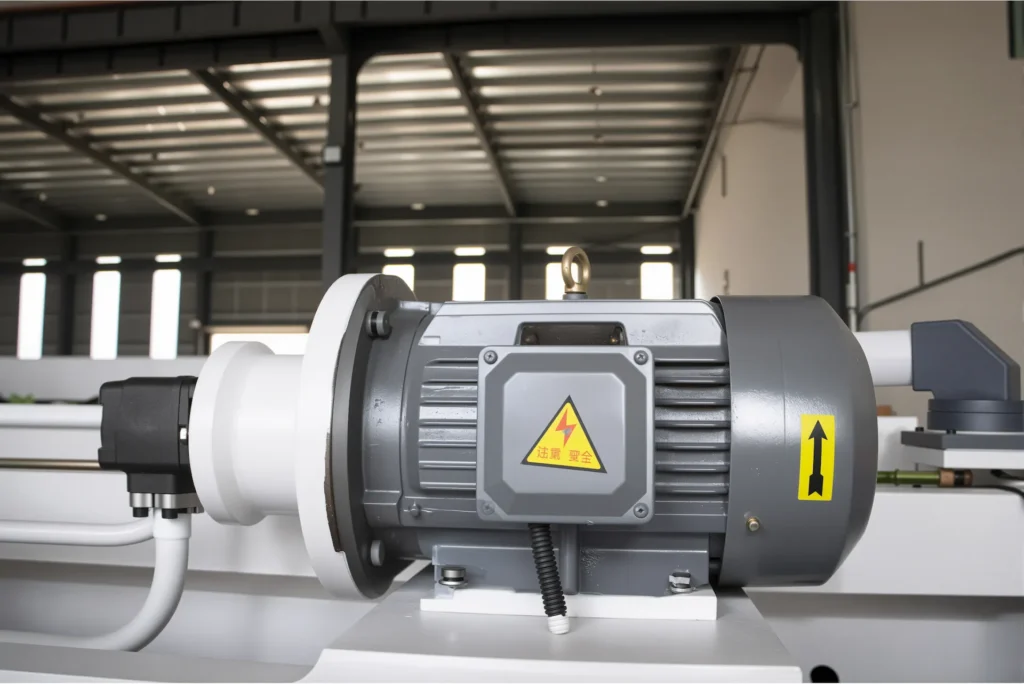
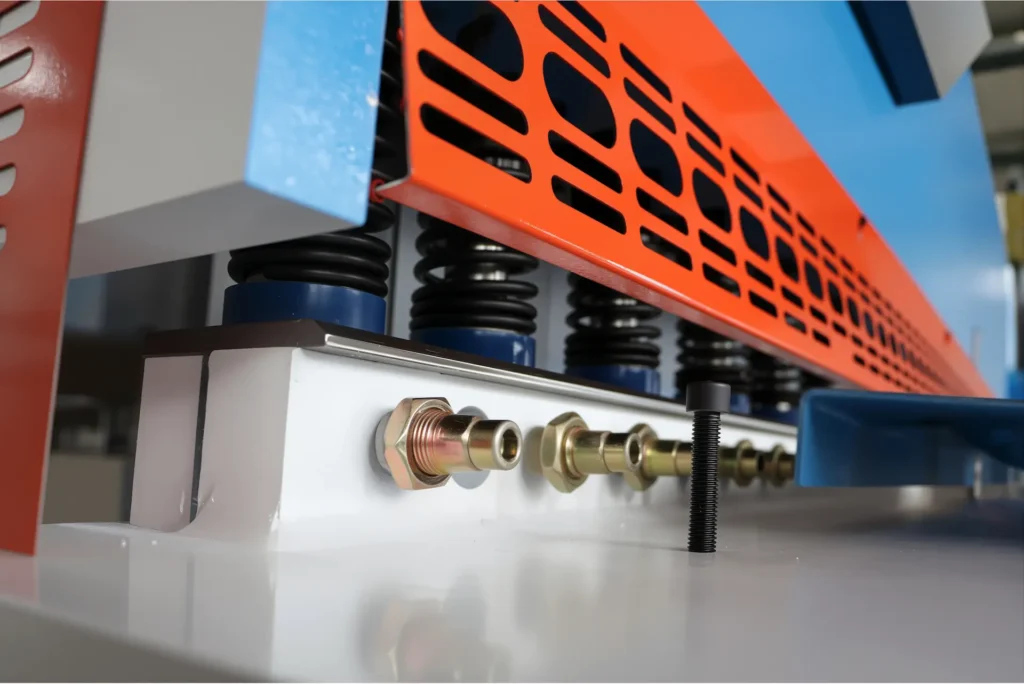
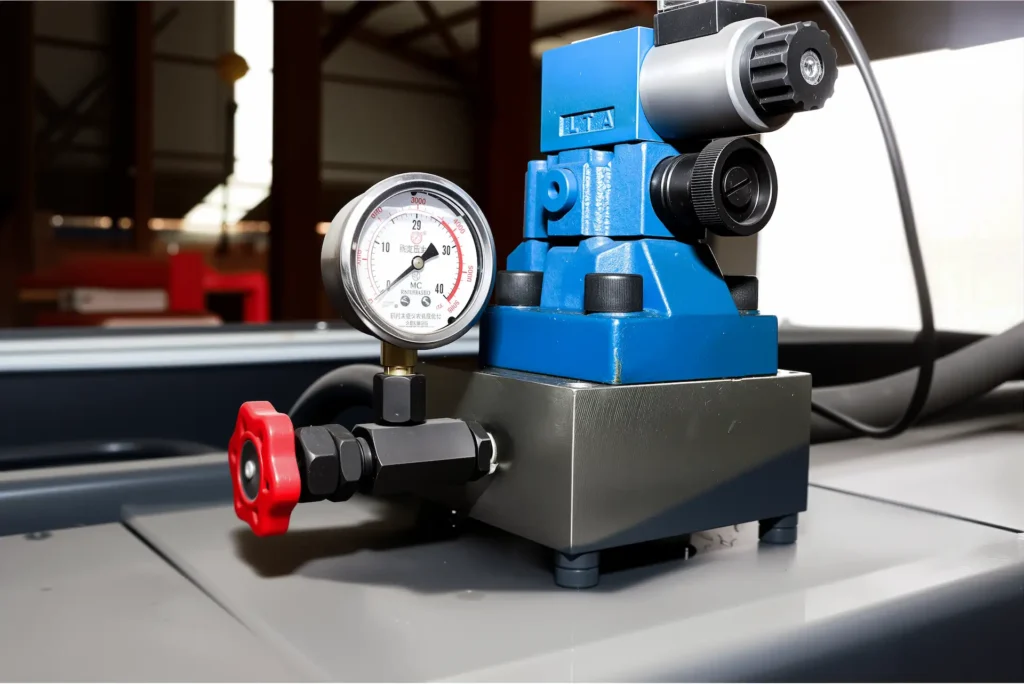
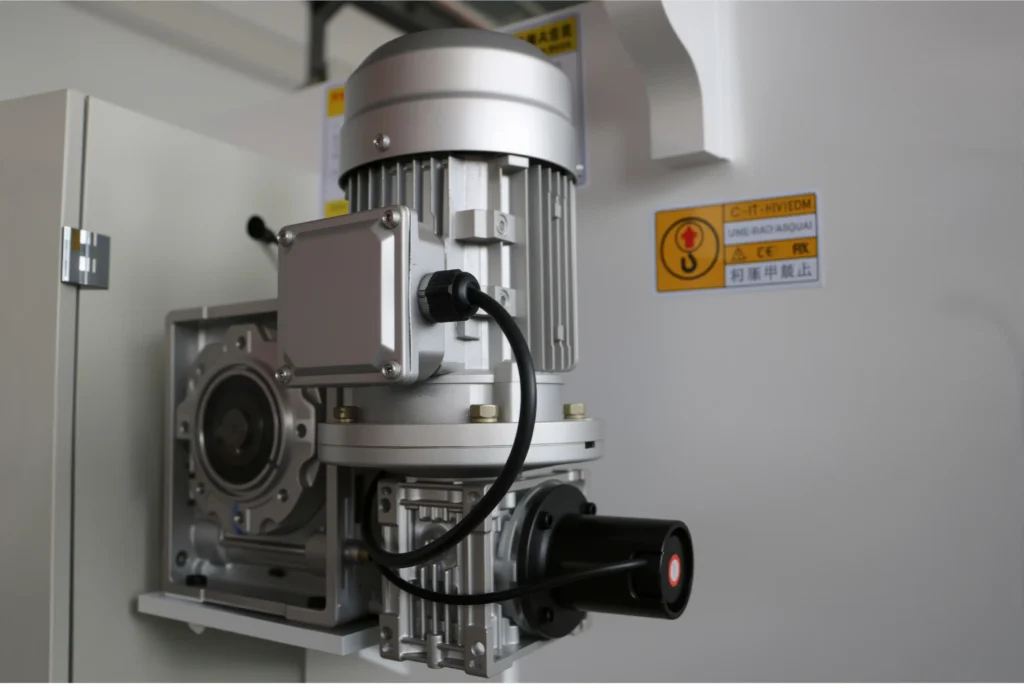
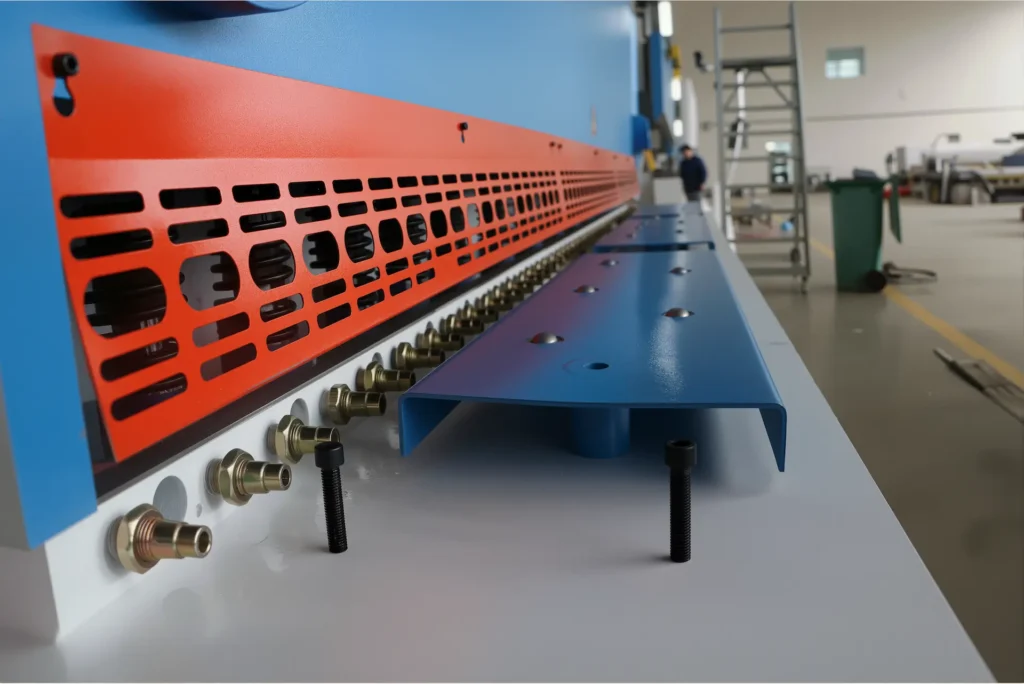
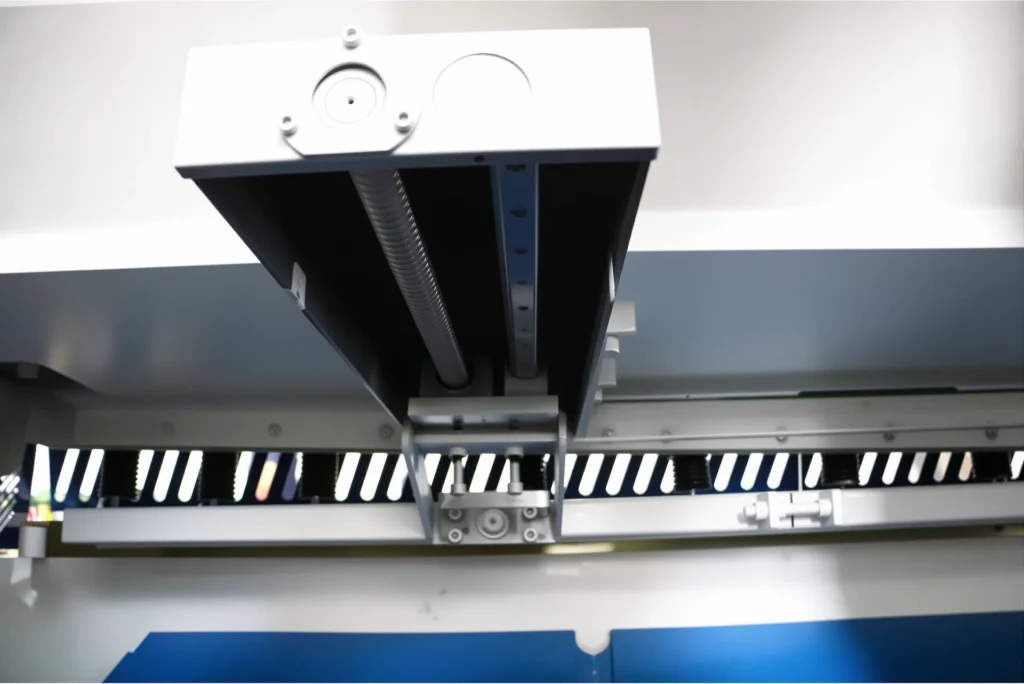
Advantage:
- Welded steel plate structure with high rigidity.
- Structural components are rust-proofed using sandblasting and coated with anti-rust paint.
- BGA is designed with a manual lifting function, facilitating the shearing of extra-long sheets.
- Multi-step programming function enables automatic operation and continuous positioning of the back gauge, achieving precise automatic adjustment of the back gauge position.
- Shearing technology function displays the shearing count in real-time, with power-off memory for back gauge position, programs, and parameters.
- Real-time display of the back gauge position.
- Back gauge employs a ball screw, ensuring high positioning accuracy and enhanced machining precision of the machine.
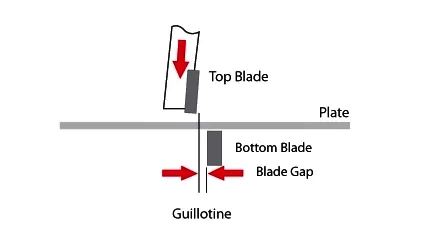